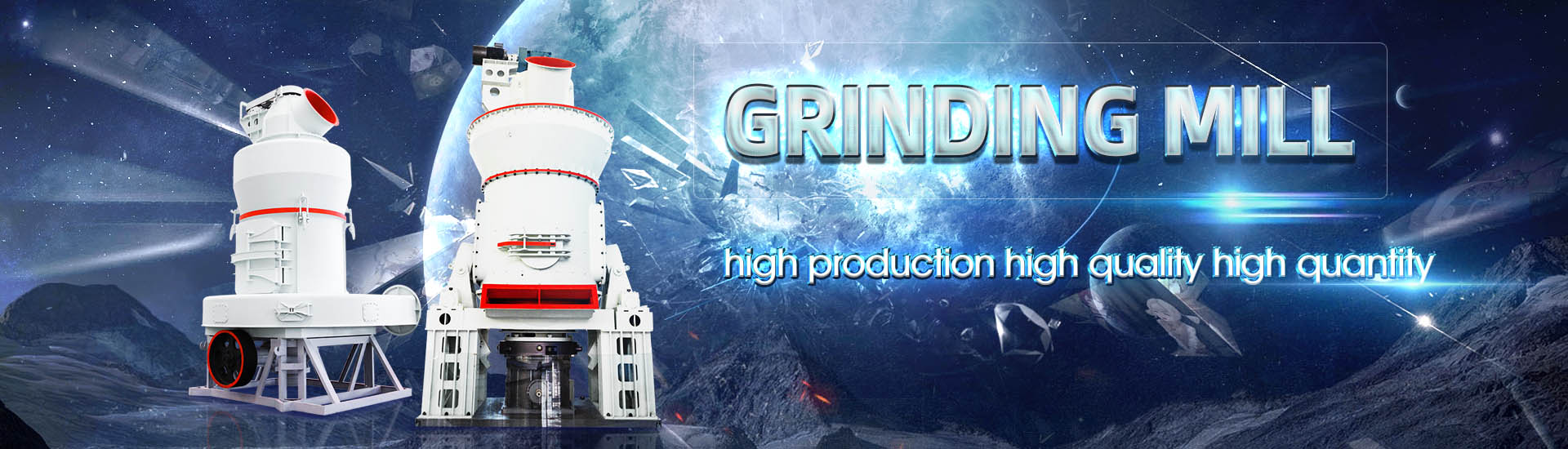
Concentration of rotary kiln coal powder
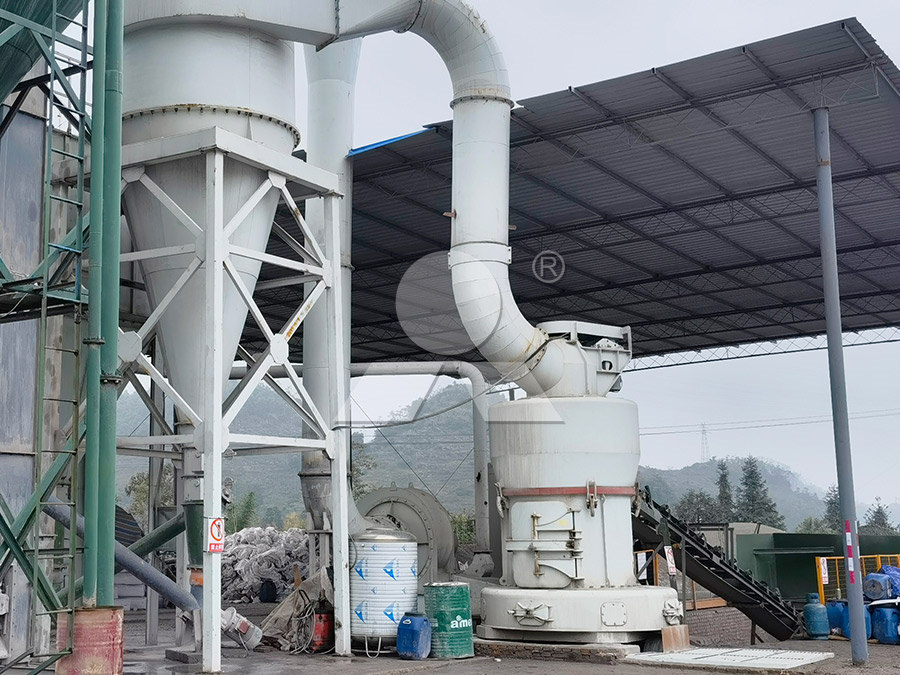
Modeling of Pulverized Coal Combustion in Cement Rotary Kiln
Combining the models of gassolid flow, heat and mass transfer, and pulverized coal combustion, a set of mathematical models for a fullscale cement rotary kiln were established1999年1月1日 A mathematical model is described for the numerical prediction of the distribution of velocity, temperature, species concentration and particle trajectories in an axisymmetric rotary cement(PDF) Modeling coal combustion in a rotary cement 2021年8月17日 Deposit formation on the lining of coalfired rotary kilns is affected by the combined influence between the quality of the green pellets, the composition of coal ash, the combustion efficiency of pulverized coal, roasting The Deposit Formation Mechanism in CoalFired 2022年5月24日 In the present study, CFD were used to investigate the effect of a new type of rotary kiln on the velocity field, temperature field, material component distribution, and NOx Numerical simulation of pulverized coal combustion in rotary kilns
.jpg)
Characterization and comparison of deposits in a coalfired rotary
2022年5月1日 The formation deposit problem becomes more severe for iron ore fluxed pellet production by the graterotary kiln process, especially for high silica iron ore and when 2023年1月1日 In this paper, the effects of pulverized coal mixed air combustion and pulverized coal mixed O2/CO2combustion on the velocity field, temperature field, CO2and NOx concentration distributionNumerical simulation of pulverized coal combustion in 2021年8月17日 In order to implement measures to ensure the efficient production of pellets by coalfired rotary kilns, the mechanism and influencing factors on the deposit formation were reviewed The(PDF) The Deposit Formation Mechanism in CoalFired The predicted results indicated that the improved model accounts for the thermal enthalpy of the clinker formation process and can give more insight (such as fluid flow, temperature, etc,) from Modeling of Pulverized Coal Combustion in Cement Rotary Kiln
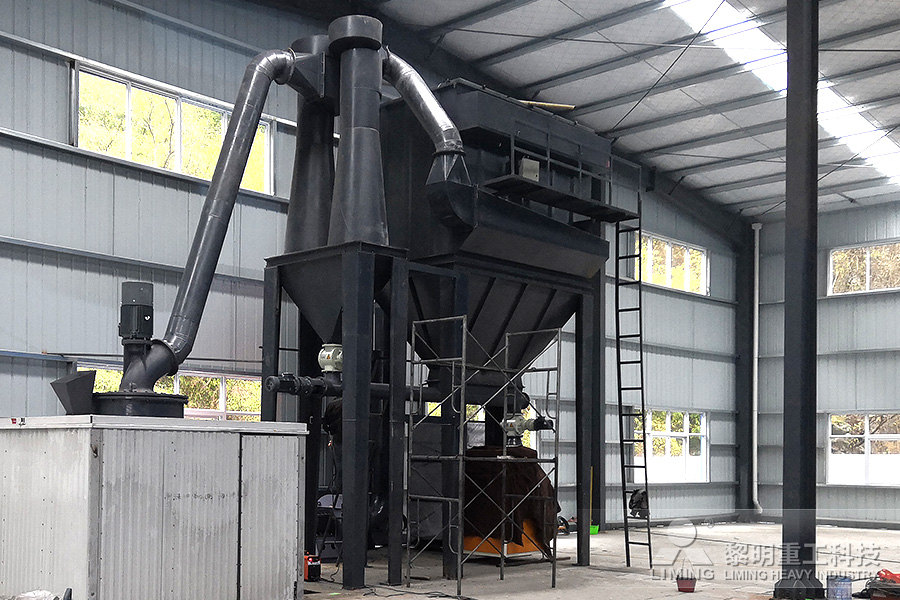
Particle motion simulation and pulverized coal injection
2022年3月16日 The rotary kiln DRI production is a typical coalbased reduction process, with mixed powder pellets (pellets of mixed titanomagnetite concentrate powder, reducing agent 2024年5月28日 The issue of ring formation in rotary kilns poses a significant obstacle to the efficient and costeffective production of oxide pellets This study focuses on sampling and Inhibiting the Accretion in the CoalFired Rotary Kiln of HighSilica 2017年2月14日 Fig 1 Cross section of rotary kiln Coal based direct reduction process is based on the solid reducing The coal fine is blown from the discharge end for maintaining the required temperature and the carbon Coal based Direct Reduction Rotary Kiln Process – 2024年5月28日 The issue of ring formation in rotary kilns poses a significant obstacle to the efficient and costeffective production of oxide pellets This study focuses on sampling and analyzing deposit formation at various points along the longitudinal axis of a 40mlong, highsilica, pellet coalfired rotary kiln The primary factors influencing deposit formation in the kiln Inhibiting the Accretion in the CoalFired Rotary Kiln of High

Study of a full scale oxyfuel cement rotary kiln ScienceDirect
2019年4月1日 The flow and combustion in the cement rotary kiln have been simulated using the ANSYS Fluent 172 RANS code The rotary kiln model dimensions have been setup according to a full scale 3000 t/d of cement with a total length of 60 m and inner diameter of 376 m, except from the clinker sintering zone (the first 20 m from the burner end of the rotary kiln) where the 2023年2月25日 The rotary kiln is used in many solid processes, including drying, incineration, heating, cooling, humidification, calcination and reduction This widespread application can be attributed to factors such as the ability to handle varied loads, with large variations in particle size [1]The rotary kiln is a slightly inclined steel cylinder that rests on supports (bearing rollers) Rotary kiln process: An overview of physical mechanisms, models 2015年11月26日 Coproduction of DRI Powder and Semicoke from Siderite Ore and Low Rank Coal by Excessive Coalbased Direct Reduction in Rotary Kiln November 2015 ISIJ International 56(1)(PDF) Coproduction of DRI Powder and Semicoke from Siderite 2021年8月17日 rotary kiln, pulverized coal is sprayed with highpressure air and burned to provide heat for the drying, oxidation and consolidation of pellets In addition, the hightemperature(PDF) The Deposit Formation Mechanism in CoalFired Rotary Kiln
.jpg)
Numerical simulation of pulverized coal combustion in rotary
2022年5月24日 In the present study, CFD were used to investigate the effect of a new type of rotary kiln on the velocity field, temperature field, material component distribution, and NOx concentration Operation of CoalBased Sponge Iron Rotary Kiln to Reduce Accretion Formation and Optimize Quality and Power Generation Shubhajit Mondal 1, Puneet Choudhary, Sampurna Borah 1, Brahma Deo, Susil Operation of CoalBased Sponge Iron Rotary Kiln to Reduce 2019年6月4日 KONA Powder and P article Journal, Vol and axial concentration profiles in the gas and solids, Minimum response time of a large coal fired rotary kiln (80 m in length) (PDF) Operation of CoalBased Sponge Iron Rotary Kiln to 2016年4月1日 In order to clearly reveal coal combustion behaviors and quantitatively evaluate using coal in rotary kiln, combustion behaviors of four coals (C13, C23, C32 and C6 coals) and their blended coals Numerical Simulation of Oxycoal Combustion in a Rotary Cement Kiln
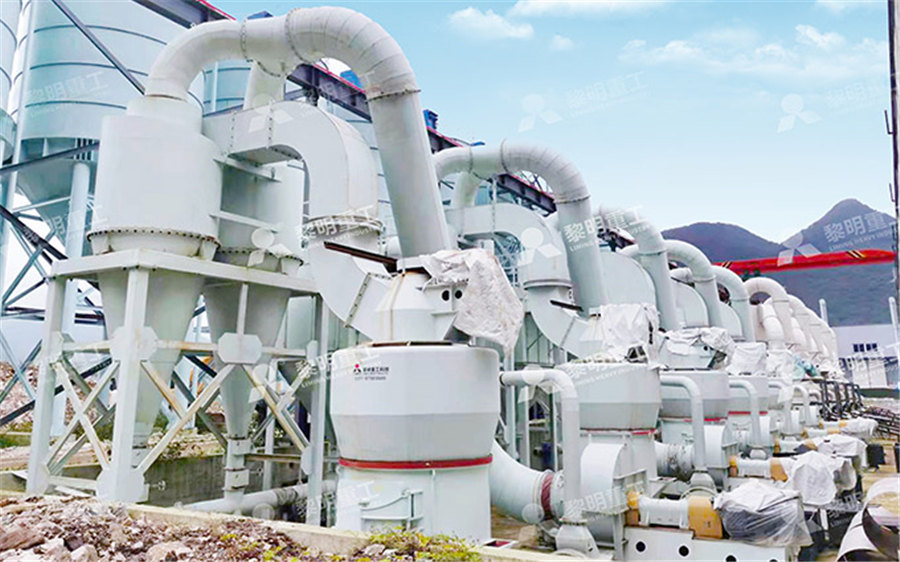
Particle motion simulation and pulverized coal injection
2022年3月16日 The production process of direct reduced iron from titanomagnetite by coal reduction in air in rotary kiln is a key step in the extraction of titanium and iron This process is conducive to alleviating the stocking problem of a large amount of Tibearing blast furnace slag The relationships between particle movement and pulverized coal injection combustion in 2020年4月14日 There are different traditional calcination processes of kaolin, eg, fixed bed process (such as tunnel kiln, down flame kiln, shuttle kiln, push plate kiln and heat preservation cylinder), moved bed process (such as shaft kiln, rotary kiln and multilayer open hearth furnace) [1,2,3,4]But, there are more or less intractable disadvantages in these modesResearch and Design of Suspension Calcining Technology and Download scientific diagram Temperature Distribution in Rotary Kiln 422 Species concentration The fuller the pulverized coal combustion in rotary kiln, the smaller the volume fraction of CO Temperature Distribution in Rotary Kiln 422Operation of CoalBased Sponge Iron Rotary Kiln to Reduce Accretion Formation and Optimize Quality and Power Generation Shubhajit Mondal 1, Puneet Choudhary, Sampurna Borah 1, Brahma Deo, Susil Operation of CoalBased Sponge Iron Rotary Kiln to Reduce
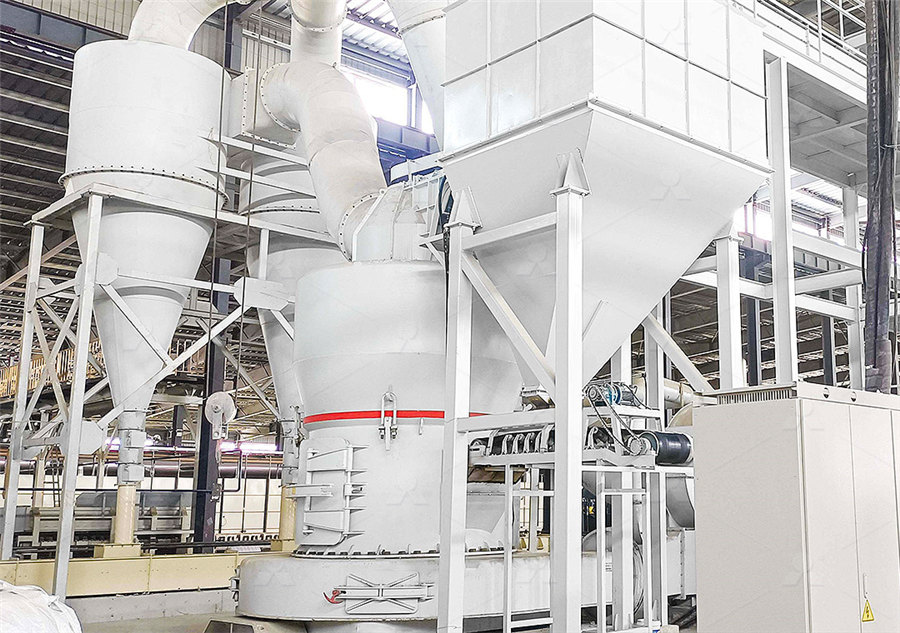
Advanced Process Control for Clinker Rotary Kiln and Grate Cooler
2023年3月3日 The cement industry includes energyintensive processes, eg, clinker rotary kilns and clinker grate coolers Clinker is obtained through chemical and physical reactions in a rotary kiln from raw meal; these reactions also involve combustion processes The grate cooler is located downstream of the clinker rotary kiln with the purpose of suitably cooling the clinker behaviors However, the thermal reaction process of coal in a rotary kiln has not been clearly understood Mathematical modeling of the coal activation process in rotary cylindrical kiln Carlos Z Oliva, Enrique Torres Tamayo , Alexandra O Pazmiño, Edwin R Pozo, Marco A Ordoñez, Sócrates M Aquino and Luis S Choto AMathematical modeling of the coal activation process in rotary2019年8月1日 Temperature Distribution in Rotary Kiln 422 Species concentration The fuller the pulverized coal combustion in rotary kiln, the smaller the volume fraction of CO in the kilnNumerical Simulation of OxygenEnriched Combustion of LowQuality Coal Download scientific diagram Schematic representation of a typical rotary kiln incinerator with flue gas treatment (Indaver, Antwerp, Belgium) [40] from publication: Hazardous waste incineration Schematic representation of a typical rotary kiln incinerator
.jpg)
Modeling of Pulverized Coal Combustion in Cement Rotary Kiln
2006年9月6日 In actual production, the oxygen concentration in rotary kiln can be adjusted more flexibly to meet the combustion needs of different coal types in kiln and realize oxygenenriched combustion 2022年5月1日 Replacing coalbased (rotary kiln and coal gasifier) DRI processes with NGbased process reduces the life cycle GHG footprint of DRI by ∼33–41% in the analyzed base cases The life cycle GHG emissions of the coal gasifier and the rotary kiln DRI processes are noted to Comparative life cycle assessment of natural gas and coalbased 2015年4月20日 In conventional coal based sponge iron plant, Fig 1, kiln feed (Stream no 1), which consists of iron ore, feed coal and dolomite, is fed to the rotary kiln (RK) A separate conve yor collects (PDF) Energy survey of the coal based sponge iron coal rotary kiln Prior art date rotary kiln coal powder injection of the prior art was all that air blast directly blows and sprays electric coal fuel in the past, and the concentration ratio of smelting process P in the ferronickel product reaches more than 4 times, CNU Rotary kiln for producing ferronickel from
.jpg)
Effect of flue gas recirculation during oxyfuel
2014年1月1日 ated by the combustion of coal in a rotary kiln oxygen is fed to the kiln at a high concentration Powder Technol 2008;182: 466 e 73Coal Pyrolysis in a Rotary Kiln: Part II Overall Model of the Furnace ´ FABRICE ´ PATISSON, ETIENNE LEBAS, FRANÇOIS HANROT, DENIS ABLITZER, and JEANLEON HOUZELOT In order to simulate coal pyrolysis in a rotary kiln in the steadystate regime, a mathematical model has been developed which calculates the temperature profiles in the charge, the gas, and the (PDF) Coal pyrolysis in a rotary kiln: Part II Overall model of the 2021年4月1日 Rotary kilns are widely used in industry to perform several different operations When numerically modeling such systems, a common simplification is to neglect the residence time distribution of Influence of Particle Residence Time Distribution on the Biomass 2019年4月18日 Hazardous waste output in the world is increasing every year To achieve higher efficiency and lower pollution, the incineration technology for hazardous waste needs to be studied furtherHazardous waste incineration in a rotary kiln: a review
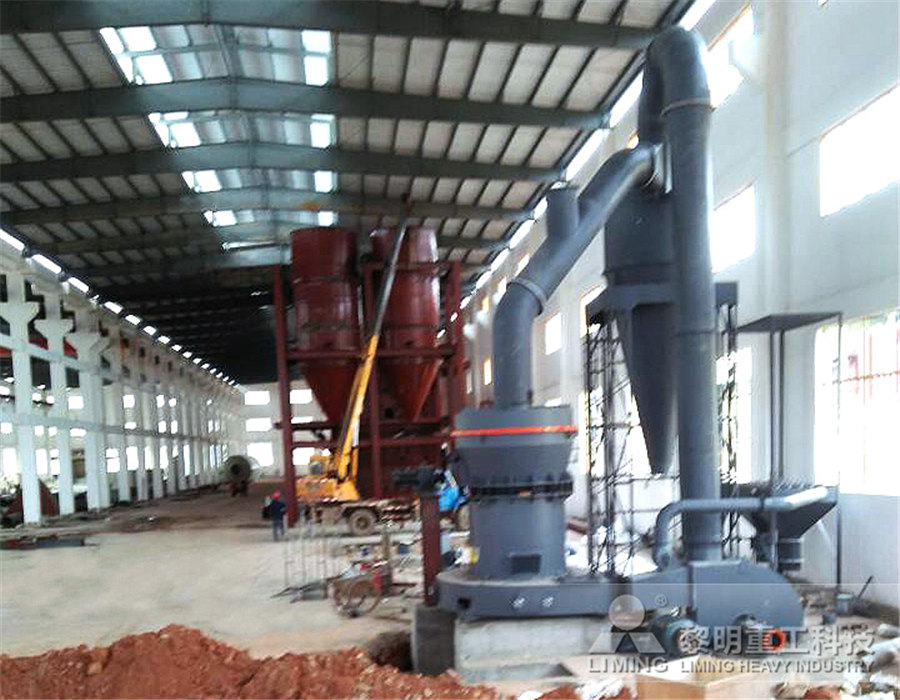
(PDF) Improving the rotary kilnelectric furnace process for
2021年9月16日 2 Coal mass flow rate Coal 10 Sum of other elements concentration in fresh mineral slagi 3 Calcine mass flow rate cal 11 Iron concentration in the calcine Feo 4 Natural gas volumetric flow 2009年10月1日 Ash melting characteristics of five coals up to 1873 K were characterized using Thermomechanical analysis (TMA) to predict their ash deposition tendency during coal combustion in a rotary kiln Forming Mechanism of Rings in RotaryKiln for Oxidized PelletKEY WORDS: siderite; low rank coal; coalbased direct reduction; DRI; semicoke; rotary kiln obtained sponge iron powder with iron grade in range of 8485%–8850% and metallization degree above 90% after magnetic separation of coalbased reduction of siderite in a fixed bed reactor Wei7) crushed the siderite ore to −2 mmCoproduction of DRI Powder and Semicoke from Siderite Ore 2020年2月14日 Direct reduction of lowgrade iron ore pelleted with coal was investigated using a pilotscale rotary kiln The evolution of the iron minerals, the strength of the pellets, and the emission Highly Efficient Beneficiation of LowGrade Iron Ore via Ore–Coal
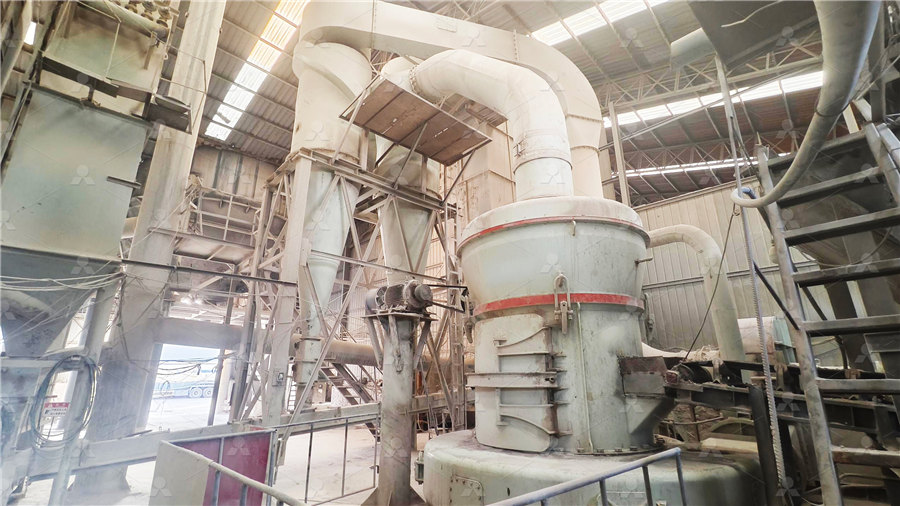
(PDF) Operation of CoalBased Sponge Iron Rotary
PDF On Jan 1, 2019, S Borah and others published Operation of CoalBased Sponge Iron Rotary Kiln to Reduce Accretion Formation and Optimize Quality and Power Generation Find, read and cite 2019年12月1日 Finally, the concentration of oxygen, Contour plot of rotation rate and stone feed rate impact on rotary kiln profit rate with a coal feed rate of 68 kg/s and air flow rate of 120 m 3 / s Powder Technol, 154 (2–3) (2005), pp 125131 View PDF View article Google ScholarModel predictive control of a rotary kiln for fast electric 2021年9月30日 PDF For two bituminous coalfired power plants with 500 MW and pulverized coal combustion type, the concentration of PM total , >PM 10 , PM 2510 , APH Rotary regenerative heat exchanger(PDF) Comparison of PMtotal, PM10, PM25, NOx, and SO2Recent developments and prospects of dioxins and furans remediation Ravichandran Rathna, Ekambaram Nakkeeran, in Journal of Environmental Management, 2018 41 Rotary kiln incineration The most commonly used and versatile technique ideal for the treatment of wastes includes a combination of solid, sludge and liquid waste streams is rotary kiln incinerationRotary Kiln Incinerator an overview ScienceDirect Topics
.jpg)
Coal Fuel Rotary Kiln with Various Output and Length for Sale
Coal fuel rotary kiln or coalfired rotary kiln is a kind of rotary kiln equipment that uses coal as fuel The fuel types of rotary kiln include gas (gasfired rotary kiln), liquid (oilfired rotary kiln), and solid or powderBecause coal is the cheapest fuel compared with other fuels, coalfired rotary kiln is widely used in the world2012年5月1日 In order to simulate coal pyrolysis in a rotary kiln in the steadystate regime, a mathematical model has been developed which calculates the temperature profiles in the charge, the gas, and the (PDF) Coal pyrolysis in a rotary kiln: Part II Overall model of the 2016年3月30日 In book: Encyclopedia of Iron, Steel, and Their Alloys (pppp 10821108) Chapter: i) Direct Reduced Iron: Production; Publisher: CRC Press, Taylor and Francis Group, New York(PDF) i) Direct Reduced Iron: Production ResearchGate2023年7月3日 Dephosphorization is essential for utilizing highphosphorus iron ore (HPIO), and this work prepared reduced iron powder via reductive roasting in a semiindustrial rotary kiln follower by Preparation of Reduced Iron Powder from High Phosphorus Iron
.jpg)
Mathematical modeling of the coal activation process in rotary
2019年5月8日 Three coals having combustion characteristics of suitable ignition temperature (745–761 K), DTGmax (1420–1572%/min), and burnout time (745–810 min) were analyzed in a rotary kilnAn Acad Bras Cienc (2017) 89 (4) Anais da Academia Brasileira de Ciências (2017) 89(4): 31233136 (Annals of the Brazilian Academy of Sciences) Printed version ISSN 00013765 / Online version Dynamic Analysis of the Temperature and the Concentration