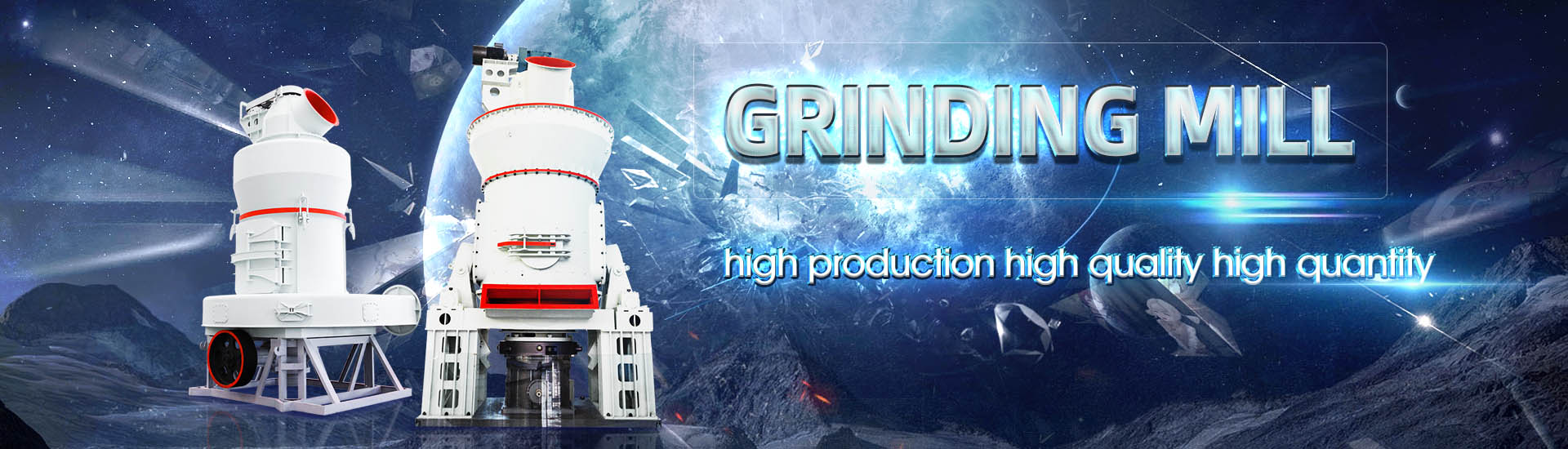
Cast iron pouring ore millCast iron pouring ore millCast iron pouring ore mill
.jpg)
The Melting, Holding and Pouring Process – Energy and Process
Fig 1 Overview of cast iron melting and pouring processes As a matter of fact, cast iron materials are melted chiefly in cupola or inductiontype furnaces today while rotary furnaces Fascinating 9 minutes from the Pilsen Steel foundry You can seea real process of the transport and pouring of an iron castingExcellent show and a perfect cPilsen Steel pouring of an iron casting YouTubeThere are two basic methods for pouring iron Tilt Pouring (pouring over lip) and Bottom Pouring (pouring with stopper rod and nozzle) There are several variations of both systems and both Advanced Pouring Technology and Temperature Control for In this article we will discuss about: 1 Manufacture of CastIron 2 Composition of CastIron 3 Types 4 Properties 5 Uses 6 Castings 7 Types of Castings 8 Characteristics of a Good CastIron: Manufacture, Composition, Types, Properties and Uses
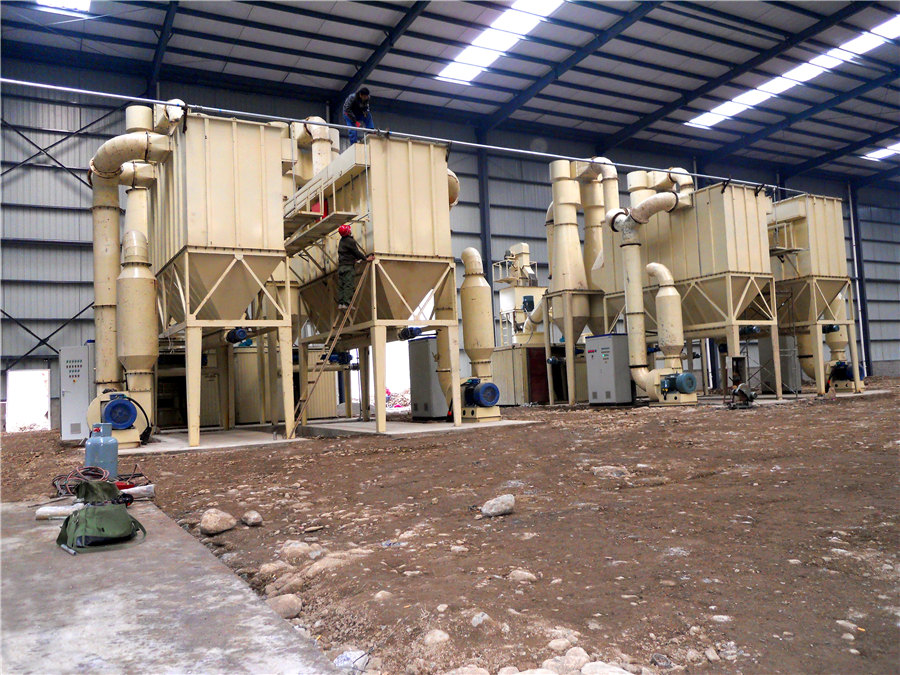
Cast Iron Explained: How's It Made, Casting Methods, Types and
Cast iron is made by melting iron and adding carbon and other elements to the molten metal, which is then poured into a mold to cool and solidify Here are the basic steps involved in 2018年4月16日 The work of melting and pouring metal looks like scenes out of the history books, but it is where some of the most interesting science is happening The manufacture of Metal Melt Pour: Life of a Casting Reliance Foundry2024年4月15日 Iron castings are robust products born from the fusion of iron and carbon, boasting a higher carbon content than steel Ranging from 2 to 43 percent, this carbon Plymouth Foundry: Mastering Traditional Principles of Iron Casting Topics include the structure and operation of the cupola used to melt the iron and the ladles used to pour it A Glossary and photos of melting and pouring operations are includedMelting and Pouring the Iron Mechanical Banks
.jpg)
Iron Ore Processing, General SpringerLink
2022年10月20日 Making iron and steel from iron ore requires a long process of mining, crushing, separating, concentrating, mixing, agglomeration (sintering and pelletizing), and PDF On Nov 1, 2020, HongNga Thi Pham published Effect of Heat Retention Time and Pouring Temperature on Graphite Shape and Mechanical Properties of Gray Cast Iron Find, read and cite all the (PDF) Effect of Heat Retention Time and Pouring2021年12月20日 Brazilian cast iron necklace inspired by the fashion known as Berlin iron, early 19 th century (Santos, 2021) With permission from Irina Aragão and Anais do Museu paulista (Brazil)(PDF) Cast Iron: A Historical and Green Material 2015年7月23日 Numerical relation of cast iron chill characteristics (distance of chilled layer H and volume quota of ledeburite in it Qл ) with its carbon equivalent СE was investigaredEffect of Pouring Temperature in Chilled Cast Iron
.jpg)
Cast Iron and Wrought Iron: What’s the Difference?
2023年1月9日 Some engineers and designers might think “cast iron” refers to early iron work, or that all early iron work was “wrought,” or that both may be true They would be wrong2018年4月16日 Smelting is the process of removing a metal element from mined ores Most metals are found as veins in rocks, or as parts of other elements Smelting is the first step of extraction Melting is what is done with metal alloys or pure metals Scrap is melted, ore is smelted Pig iron is the rough iron ingots created from iron ore smelting Blast Metal Melt Pour: Life of a Casting Reliance Foundry2022年10月20日 Iron ore handling, which may account for 20–50% of the total delivered cost of raw materials, covers the processes of transportation, storage, feeding, and washing of the ore en route to or during its various stages of treatment in the mill Since the physical state of iron ores in situ may range from friable, or even sandy materials, to monolithic deposits with hardness of Iron Ore Processing, General SpringerLinkPatterns and the Molding of Cast Iron Banks Supplement No 8: Melting and Pouring the Iron Fritz Kokesh A INTRODUCTION The article "Patterns and the Molding of Cast Iron Still Banks"1 touched on melting and pouring the iron This supplement provides details about the equipment used and its operation TopicsMelting and Pouring the Iron Mechanical Banks
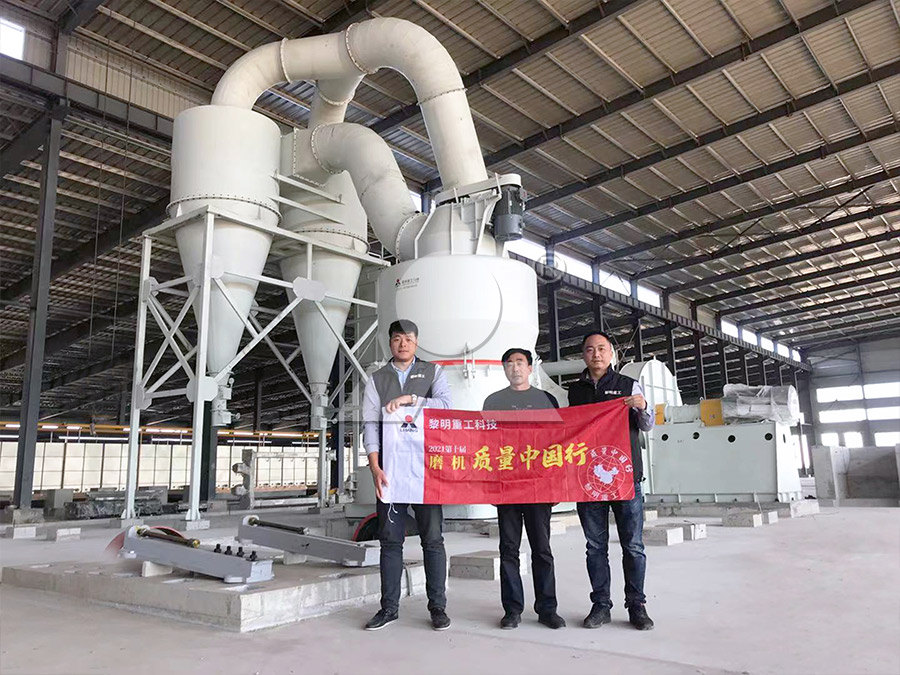
Ask a Metallurgist: Wrought Iron vs Cast Iron Metal Casting Blog
2020年2月14日 Both ductile and cast iron castings are produced by pouring molten iron into molds Corrosion considerations Cast iron and wrought iron are both susceptible to corrosion when bare surfaces are exposed to oxygen in the presence of moisture This can be challenging for outdoor environments with nearconstant exposure to precipitation and humidityCast iron is derived from pig iron, and while it usually refers to gray iron, it also identifies a large group of ferrous alloys which solidify with a eutectic The colour of a fractured surface can be used to identify an alloy White cast iron is named after its white surface when fractured, due to its carbide impurities which allow cracks to pass straight throughCast Iron Metallurgy for Dummies2017年10月17日 Figure 1: Steelmaking byproducts for blast furnace (BF), basic oxygen furnace (BOF) and electric arc furnace (EAF) processes Source: World Steel Association (worldsteel) The first step in the production of steel or cast iron alloys is the reduction of iron ore—which contains iron oxide and gangue or mineral impurities—to unrefined, reduced iron formFrom Ore to Iron with Smelting and Direct Iron Reduction2020年11月1日 Cast iron is most commonly made from a mixture of iron, steel railroad ties, recycled steel, castings shaken out from earlier production, and pig iron (aka crude iron, an intermediate product of the iron industry made by The Ultimate Cast Iron Guide Minimalist Baker
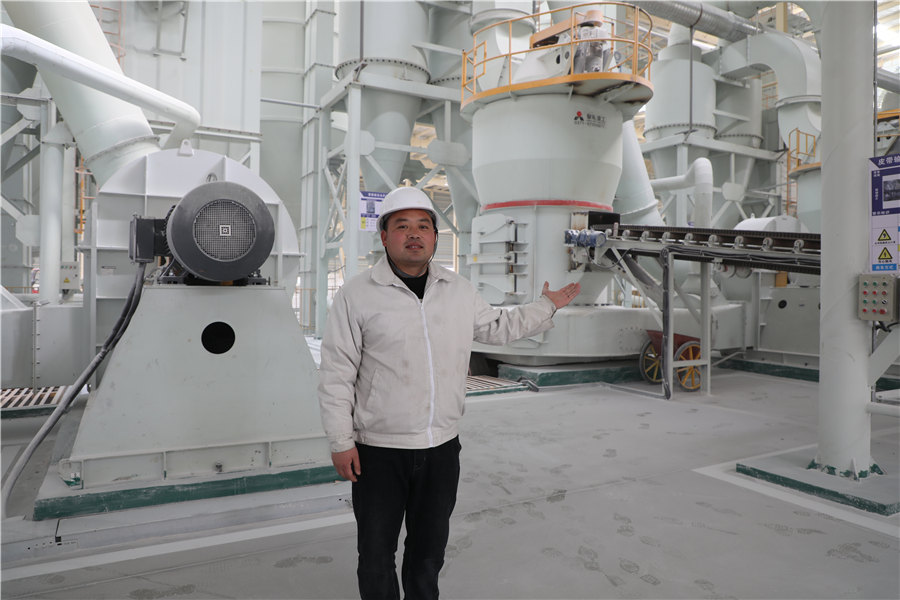
Autopour Furnace Fomet srl
2018年7月6日 In 2016, FOMET Srl, world leader in auto pouring technology of cast irons introduced their innovative “PEP” Autopour (Powered Easy Pour) In order to meet modern foundry needs FOMET have designed a unit with the The molten cast iron pouring system is shown in the diagram of Figure 201 and the photograph of Figure 2 The pouring apparatus moves along a line of molds made by a molding machine First, the system moves along the line to search the sprue of an unpoured mold The beak is Chapter 52 Automatic Pouring System for Cast Iron2017年5月29日 The molten cast iron is led into moulds of required shapes to form what are known as cast iron castings and slag is removed from the top of cast iron at regular intervals Composition of cast iron: Cast iron contains about 2 to 4 percent of carbon Manganese makes cast ironbrittle and hard, so it may be kept below 075 percentPIG IRON, CAST IRON WROUGHT IRON 2024年4月8日 Opencast iron ore mining is vital for the global economy, providing the raw material for steel production It is costeffective and allows for the efficient extraction of large ore quantities within shorter timeframes compared to underground mining However, opencast mining can have significant environmental impacts Opencast iron ore mining is essential for meeting Bibliometric and Scientometric Assessment of the Environmental
.jpg)
(PDF) i) Direct Reduced Iron: Production ResearchGate
2016年3月30日 In book: Encyclopedia of Iron, Steel, and Their Alloys (pppp 10821108) Chapter: i) Direct Reduced Iron: Production; Publisher: CRC Press, Taylor and Francis Group, New YorkDownload scientific diagram The schematic representation of the white cast iron microstructure at room temperature The darkgray areas represent the former austenite dendrites that transformed The schematic representation of the white cast iron OVERVIEW OF CAST IRON MELTING AND POURING PROCESSES The general overview of alternative processes shows the variety of paths of the molten iron from the melting furnace to the pouring location (Fig 1) Fig 1 Overview of cast iron melting and pouring processes As a matter of fact, cast iron materials are meltedThe Melting, Holding and Pouring Process – Energy and Process Cast iron has been used extensively in many industrial applications, such as water industry, for more than 150 years As a result, a large proportion of water transport and distribution pipes were predominantly made of cast iron in the past although they are being phased out by the introduction of new materialsCast Irons; Types, Properties, Applications Weldability
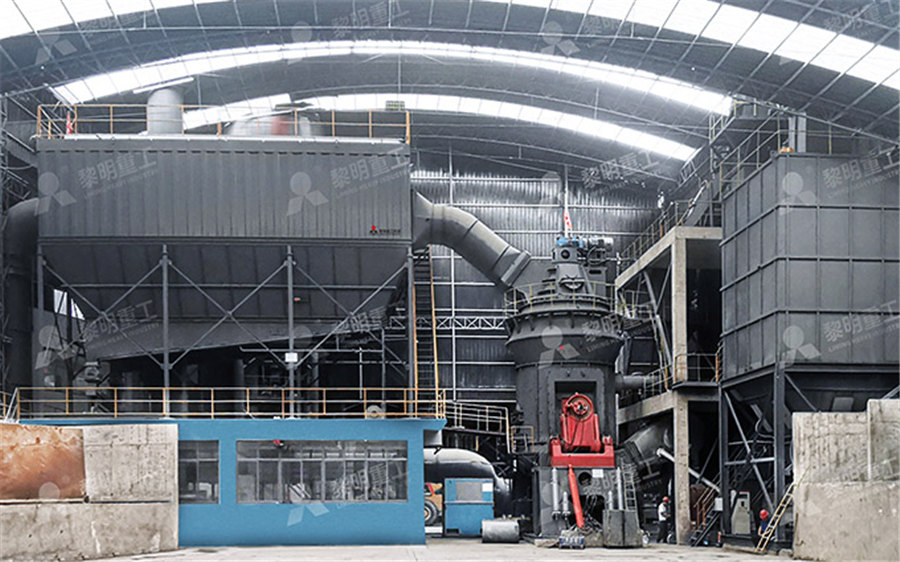
Iron Ore an overview ScienceDirect Topics
113212 IronBearing Materials Ore fines and iron concentrates make the main part of the sinter mix The grain size of ore fines and concentrates is typically 0–8 and 0–3 mm, respectivelyGrains smaller than 01 mm are not desired because they reduce the gas permeability of the bed and thus decrease the sintering efficiencyRecycled materials, such as 2017年10月10日 Roasting or calcination of the ore oxidizes some of the sulfur, phosphorus and arsenic impurities Sulfur oxide is volatile and evaporates off or is washed out Iron is mainly extracted from hematite (Fe 2 O 3) and magnetite Ironmaking 101 – From Ore to Iron with Blast Furnaces2017年9月23日 PDF Spheroidal graphite cast iron is a special variety of cast iron having carbon content more than 3% and has graphite present in compact, spherical Find, read and cite all the research (PDF) ENHANCING THE PROPERTIES OF SG CAST Iron processing Ores, Smelting, Refining: Iron ores occur in igneous, metamorphic (transformed), or sedimentary rocks in a variety of geologic environments Most are sedimentary, but many have been changed by Iron processing Ores, Smelting, Refining Britannica
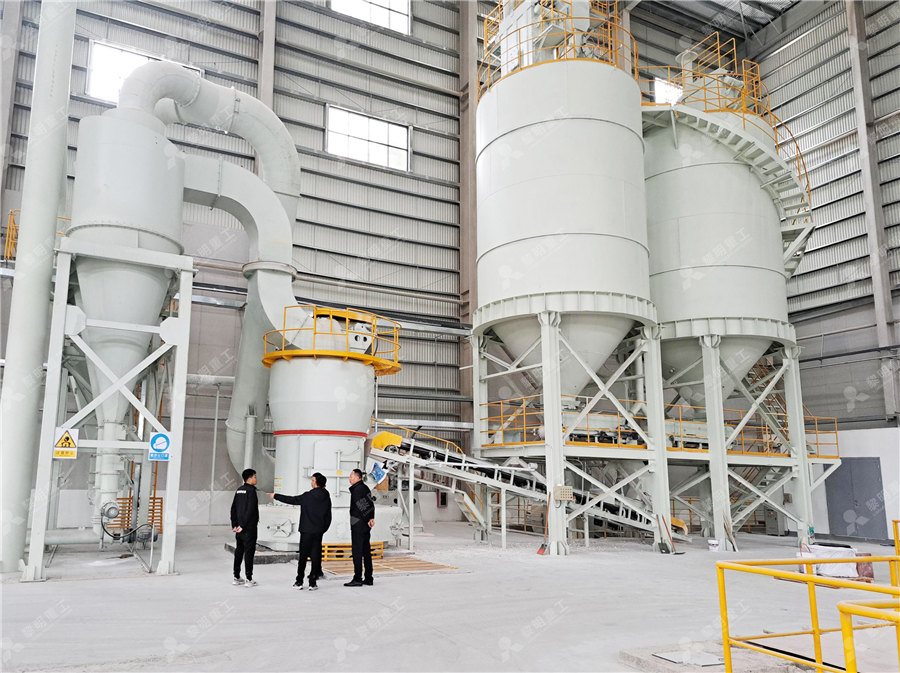
Introduction: Overview of the global iron ore industry
2022年1月1日 Turning to iron ore exports and imports, the tonnages are summarized in Table 11 for 2012 and 2018 (Australian Department of Industry, Science, Energy and Resources, 2021; US Geological Survey, 2020; United National Conference on Trade and Development (UNCTAD), 2021)As shown in Fig 13, China is the largest iron ore importing country and imported about To make cast iron, iron ore is heated in a furnace until it becomes molten White Cast Iron is used primarily for its wear resistant properties in pump housings, mill linings and rods, crushers, and brake shoes Composition: Carbon – 18 to 3%; Manganese – Cast Iron: Definition, Properties, And Uses The Engineering ChoiceBy the end of the 20th century, nonstick skillets had become more common than cast iron in most homes However, as worrying reports about the effects of chemical nonstick coatings on the environment and our health came to light, more and more cooks returned to the original “green” pan, the castiron skillet, as an alternative and rediscovered all the advantages it has to offerAll About Cast Iron America's Test Kitchen2012年1月1日 However, the studies of the pouring temperature and holding time on the mechanical properties of gray iron are very limited In [13, 14], the authors described the effect of cooling rate on Effect of Pouring Temperature and Casting Thickness on Fluidity
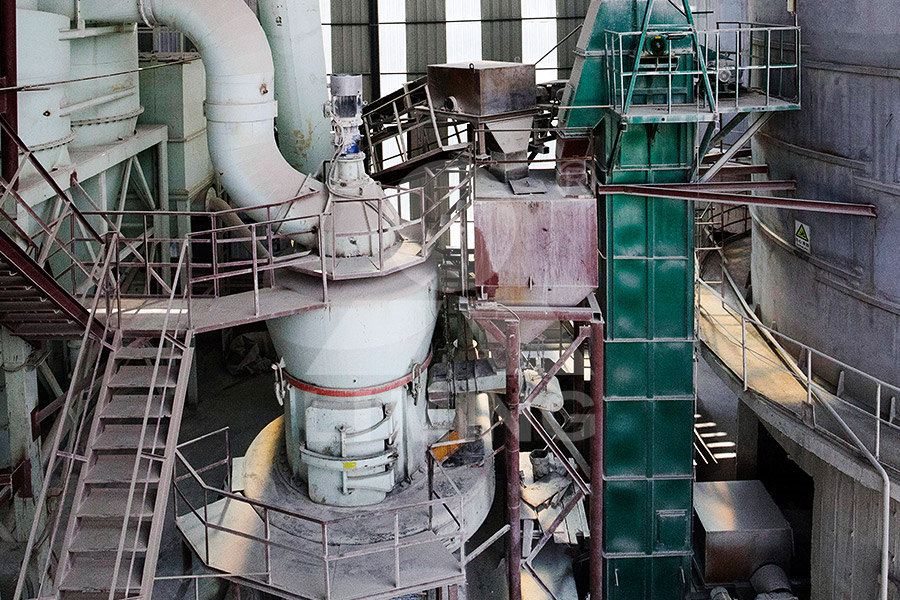
123: Metals and Ores Chemistry LibreTexts
Iron ore is reduced with coke in a blast furnace (Figure \(\PageIndex{1}\)) The blast furnace is loaded with iron ores, usually hematite Fe 2 O 3 or magnetite Fe 3 O 4, together with coke (coal that has been separately baked to remove volatile components) Air preheated to 900 °C is blown through the mixture, in sufficient amount to turn the Howdy Folks! Here's another short little taste of what it looks like to hold and pour a ladle of molten iron! This footage didn't make the cut in the finalPOV Pouring Cast Iron Tapping an Iron Furnace YouTubePDF On Oct 15, 2018, Doru M Stefanescu published A History of Cast Iron Find, read and cite all the research you need on ResearchGate(PDF) A History of Cast Iron ResearchGate2020年1月11日 Cast iron is made by melting the alloy past the melting temperature, pouring it onto a cast, and allowing the metal to cool and solidify However, before the alloy can be made, pig iron must first be produced by Wrought Iron vs Cast Iron: What They Are and
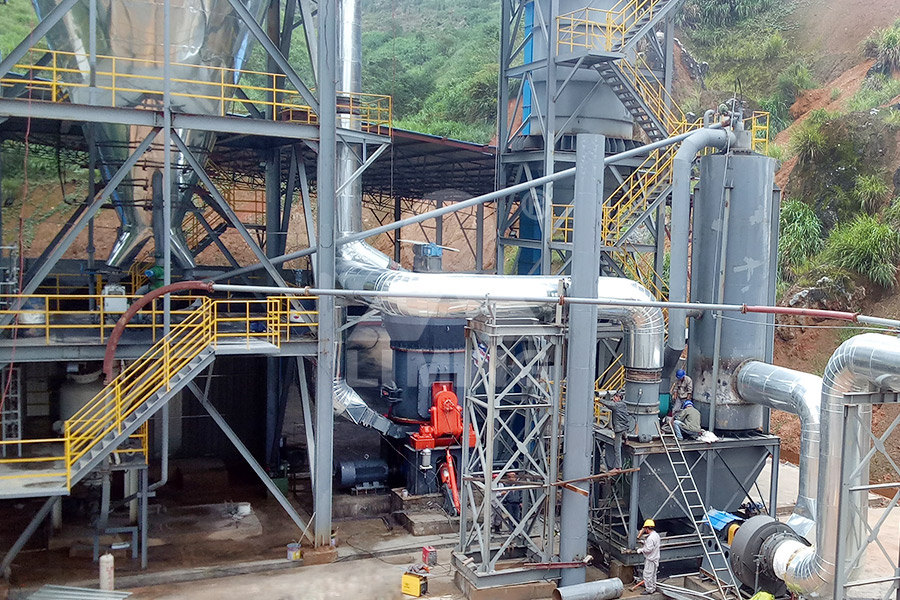
Iron ore grinding mill Grinding plants for Iron Ore
Iron ore is an important industrial source, is an iron oxide ore, a mineral aggregate containing iron elements or iron compounds that can be economically utilized, and there are many types of iron ore Among them, the iron smelting products mainly include Magnetite, siderite, and hematite and so on Iron exists in nature as a compound, and iron ore can be gradually selected after 2005年10月1日 Silicon promotes graphitization and thus increases the amount of ferrite in cast iron Moreover, results obtained by another author [19] indicate a significant effect of the chemical composition MicrostructureProperty Relationships in Cast Irons2024年11月13日 We tested leading cast iron skillets from the likes of Le Creuset, Staub, Lodge and more leading brands to bring you our tried and approved guideThe best cast iron skillets 2024: Tested and rated Tom's Guide2018年10月23日 The ore is Hematite, chemical name is iron III oxide, the chemical formula is Fe 3 O 4, It has a blood red colour, it is more easily reduced, Iron is from 5060 %, place of deposits is Oasis area (western desert) and western part of Aswan The ore is Limonite, chemical name is Hydrated iron III oxide, the chemical formula is 2Fe 2 O 33H 2 O, It has a yellow hydrated Extraction of Iron from its ores, Iron dressing, Reduction production
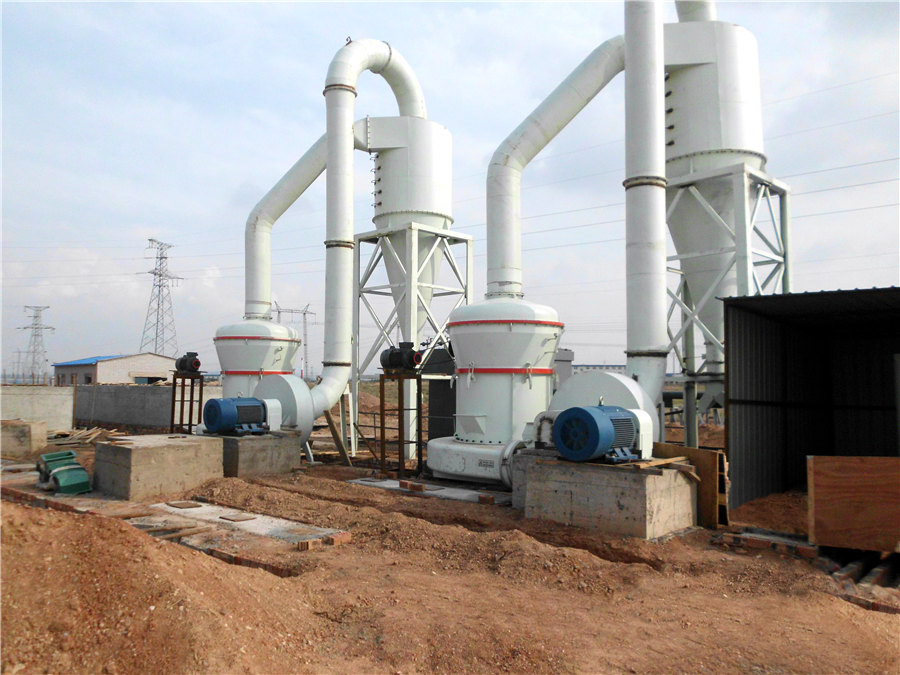
Overview of metal casting for beginners I Forge Iron
2011年12月15日 Hi all, figured I'd make my first post something useful rather than a question I know more about casting than blacksmithing, so I figured I’d help add to the casting section a little by providing a general overview of how to get started in casting, reference books, equipment needed, safety precautions, etc Hopefully this will be something that can be referenced to 2020年8月19日 Throat: zone for charging the burden [ferric charge + reductant (coke)]The blast furnace gases circulate through the throat of the furnace toward the dry and wet cleaning systems The temperature in the throat is 200–250 °C, the pressure is around 15 atm (there are blast furnaces in Russia and other countries that operate with bigger excesses of pressure), Production of Iron in the Blast Furnace SpringerLinkCast iron is made by reducing Iron Ore in a Blast Furnace The liquid iron is poured or cast and hardened into crude ingots called pigs, and the pigs are then remelted along with scrap and alloying elements in cupola furnaces and recast into molds to produce a variety of productsCast Iron Metal: Definition, Properties, And Uses Mechdaily2021年3月10日 Read this blog for a stepbystep guide to pouring in foundries, including how automatic pouring units create a safer environment for engineers Our Company pours 550,000 tonnes of metal every year This works out at roughly 1,650 tonnes a day The final products are made in castiron materials and are commonplace in How Do Foundry Pouring Units Work?