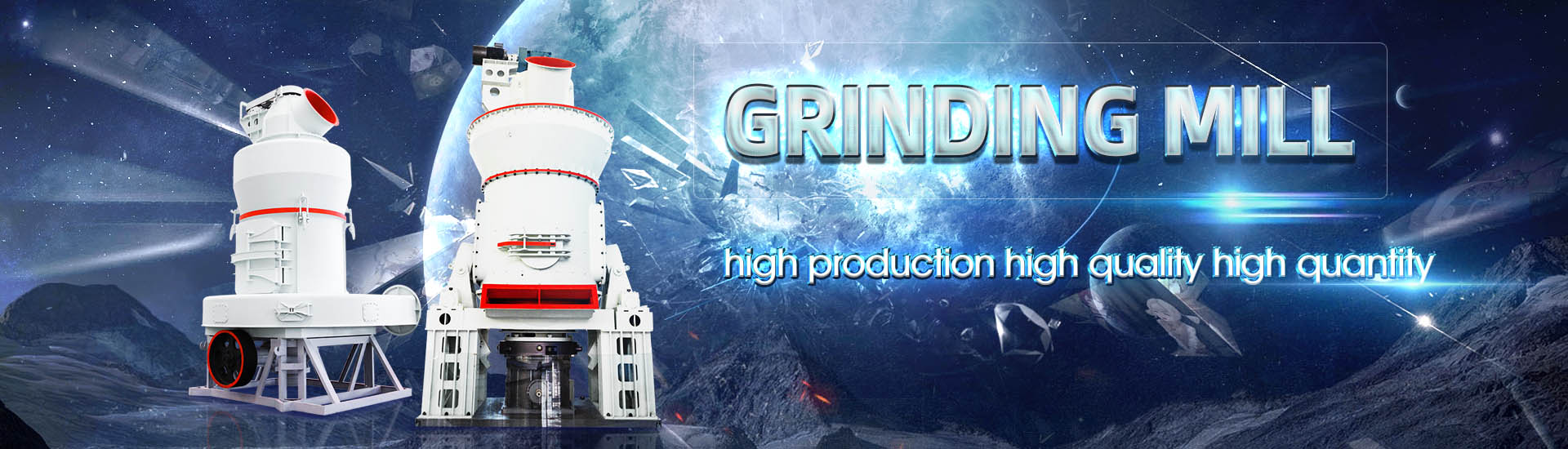
Yantai ore smelting and decomposition
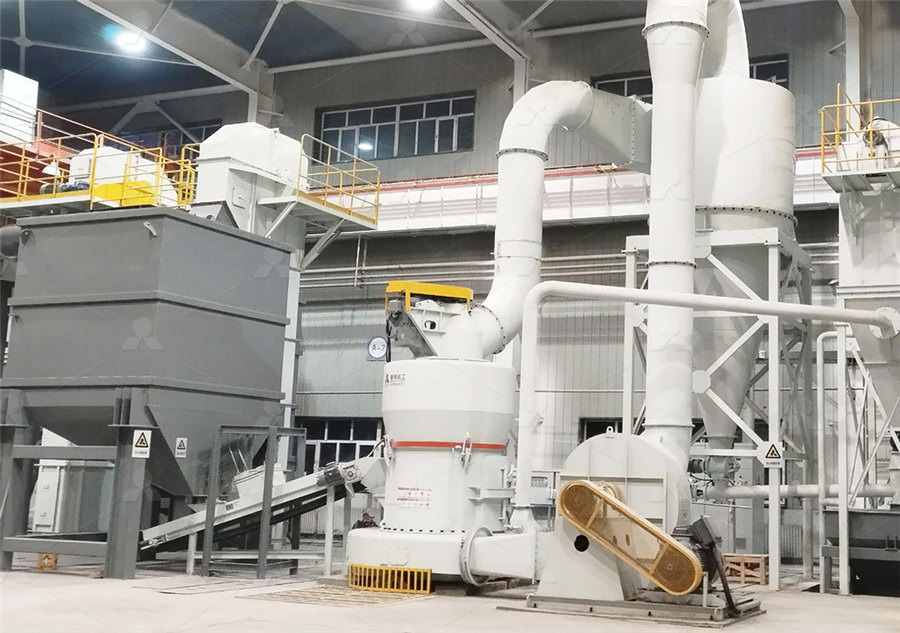
Guoyang ZHANG Doctor of Engineering Yantai University, Yantai
In this work, a revolutionary way for preparing Febased amorphous alloys from the refractory highphosphorus oolitic iron ore with the combination of smelting reduction and meltspinning Conquer low grade and difficult beneficiation smelting of gold mines; Have rich experience in design of metal, nonmetal, tailings, own many patentsDesignYantai Jinpeng Mining Machinery, ore dressing process 2015年2月6日 HIsarna is a new alternative ironmaking process of ULCOS program, which is under intensive development at EU It uses coal and fine iron ore directly as raw materials (PDF) Melting and Reduction Behaviour of Individual Fine The smelting cyclone of the HIsarna process is a complicated high temperature reactor In the smelting cyclone, the temperature is extremely high and the size of the iron ore particles is Thermal Decomposition Behaviour of Fine Iron Ore Particles J
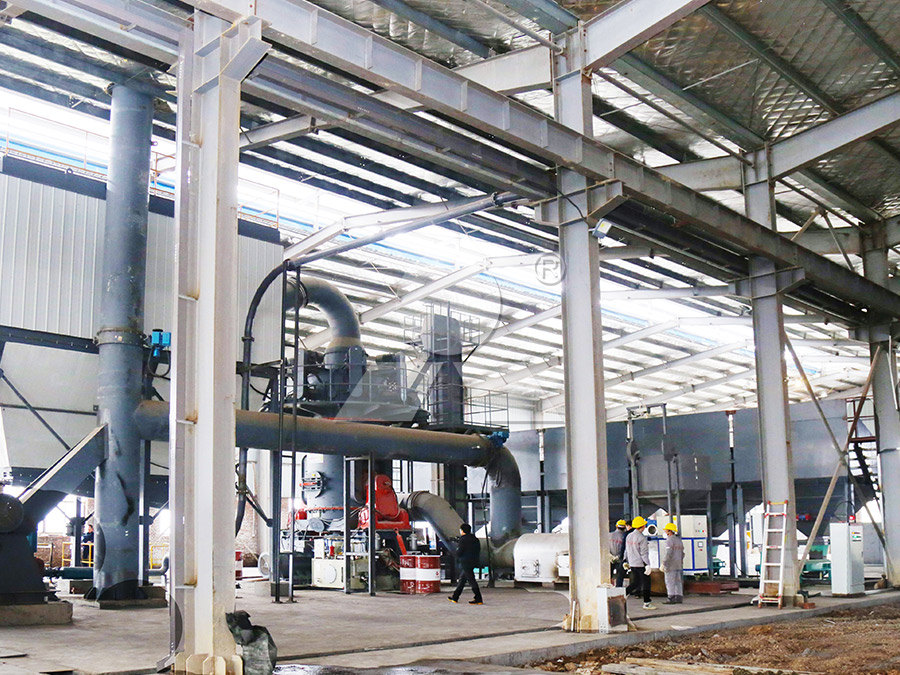
Thermodynamic modeling of antimony removal from complex
2022年12月1日 This model was also used to investigate the effect of process factors such as copper matte grade, oxygenenriched concentration, smelting temperature, and oxygen/ore 2024年9月15日 Thermal decomposition of hematite plays an important role during pelletization and the iron finebased smelting processes such as HIsarna and flash shaft smelter The Thermal Decomposition of Hematite Ore Fines in Airsmelting cyclone and SRV are highly integrated and operated as a single smelting furnace In the smelting cyclone, the fine iron ore is prereduced to a prereduction degree of about 20% Melting and Reduction Behaviour of Individual Fine Hematite Ore 2020年7月3日 This paper provides a comprehensive current review of our fundamental understanding of manganese ore smelting Process parameters and resultant cost effects are A Review of Ore Smelting in High Carbon Ferromanganese
.jpg)
(PDF) The Outotec ® Direct Zinc Smelting Process
2015年6月14日 The basic methods of obtaining zinc from ores, including pyrometallurgical (Imperial Smelting Process ISP, Kivcet, Ausmelt) and hydrometallurgical (roasting–leaching–electrowinning RLE 2014年10月31日 For the study of the thermal decomposition behavior of iron ore during smelting reduction, previous experimental methods included a thermogravimetric analysis (TGA) device, a heated horizontal Thermal Decomposition Behaviour of Fine Iron Ore ParticlesThe initial decomposition temperature of Mg2Te3O8 was 8321 °C, 8392 °C, and 8399 °C, when the O2 concentration in the carrying gas was 20%, 01%, and 00001%, respectively; 3) The The required offgas treatment capacity of different 2023年1月1日 The ore was mainly composed of pyrolusite (MnO 2 ) and calcite (CaCO 3 ) Goethite and quartz were also present in smaller quantities According to the literature [4,810,12,14,15], bixbyite Thermal upgrading of manganese ores prior to smelting
.jpg)
(PDF) Reaction Mechanism and Distribution Behavior of Arsenic in
2017年8月5日 from the SKS smelting system to the gas phase, low oxygen concentration, low ratios of oxygen/ore, and low matte grade should be chosen In the SKS smelting process, no dust is recycled, and almost2023年3月29日 DOI: 103390/met Corpus ID: ; Study on the Bath Smelting Reduction Reaction and Mechanism of Iron Ore: A Review @article{Wang2023StudyOT, title={Study on the Bath Smelting Reduction Reaction and Mechanism of Iron Ore: A Review}, author={Guilin Wang and Jianliang Zhang and Yaozu Wang and Yubo Tan and Zhen Li and Study on the Bath Smelting Reduction Reaction and Mechanism of Iron Ore Smelting is a process of applying heat and a chemical reducing agent to an ore to extract a desired base metal product [1] It is a form of extractive metallurgy that is used to obtain many metals such as iron, copper, silver, tin, lead and zincSmelting uses heat and a chemical reducing agent to decompose the ore, driving off other elements as gases or slag and leaving the metal Smelting Wikiwand2021年7月7日 Abstract: The heat recovery steam generator (HRSG) of copper smelting generates a large number of arseniccopper containing particles, and the insitu separation of arsenic and copper is of importance for cutting off environmental risk and realizing resource recovery The formation of arseniccoppercontaining particles was simulated, the method of in Formation of arseniccoppercontaining particles and their
.jpg)
Melting and Reduction Behaviour of Individual Fine Hematite Ore Particles
ing and prereduction, and a smelting reduction vessel (SRV) for final ore reduction and iron production The smelting cyclone and SRV are highly integrated and operated as a single smelting furnace In the smelting cyclone, the fine iron ore is prereduced to a prereduction degree of about 20% through thermal decomposition and reduction byMercury in Gold Processing N Ahern, in Gold Ore Processing (Second Edition), 2016 21 Oxidative Pretreatment During roasting of gold ores and concentrates, mercury is released to the gas phase, with the extent of release dependent on the mineralogical composition of the roaster feed and on the roasting conditions (temperature, roasting atmosphere and roasting time)Roasting an overview ScienceDirect TopicsDownload scientific diagram Experimental methods for the thermal decomposition of iron ore (a) TGA; (b) heated horizontal furnace; (c) hightemperature drop tube furnace from publication Experimental methods for the thermal decomposition of iron orereaction The prediction of the thermal decomposition of the ore in the open system (Fig 4) shows that the amount of the released oxygen from the ore reaches 169, 508, and 1550 L oxygen gas when the ore was decomposed to Fe 3O 4, FeO, and Fe, respectively The oxygen emission in the decomposition is less than 508 L (The oxygen isThermal Decomposition Reaction Kinetics of Hematite Ore J
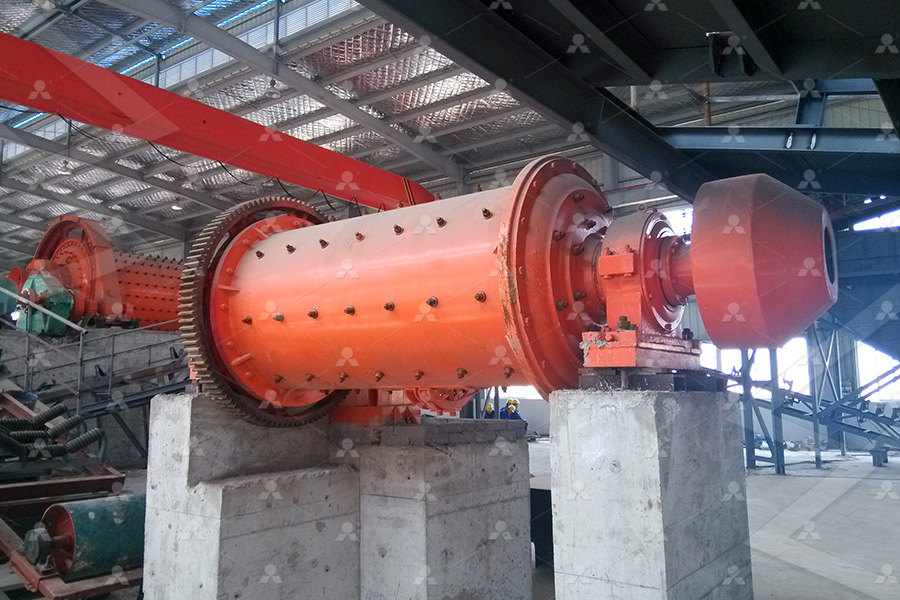
(PDF) Thermodynamic evaluation for reduction of
2018年7月27日 In the smelting cyclone of Hlsarna process, both thermal decomposition and gaseous reduction of iron ore contribute to the expected prereduction degree about 20%2023年4月5日 The blast furnace and direct reduction processes have been the major iron production routes for various iron ores (ie goethite, hematite, magnetite, maghemite, siderite, etc) in the past few decades, but the challenges of maintaining the iron and steelmaking processes are enormous The challenges, such as cumbersome production routes, scarcity of Recent Trends in the Technologies of the Direct Reduction and Smelting ing and prereduction, and a smelting reduction vessel (SRV) for final ore reduction and iron production The smelting cyclone and SRV are highly integrated and operated as a single smelting furnace In the smelting cyclone, the fine iron ore is prereduced to a prereduction degree of about 20% through thermal decomposition and reduction byMelting and Reduction Behaviour of Individual Fine Hematite Ore ParticlesCopper Smelting: To produce bronze, people became adept at smelting copper ores, a process that involves heating copperrich minerals to high temperatures Early smelting furnaces were simple clay structures fired with wood or charcoal The Iron Age and Ferrous Metallurgy:Guide to Modern Smelting Processes CED Engineering
.jpg)
Experimental Study of the Melting and Reduction Behaviour of Ore
Based on the results of thermal decomposition of iron ore particles, the individual particle reduction mechanism of hematite ore in the smelting cyclone has been investigated with the HTDF Under the studied experimental conditions, the maximum reduction degree of iron ore particle is in the range of 2330 %insitu decomposition of copper arsenate In this process, gaseous arsenic was released, and thus the separation of arsenic and copper was realized Key words: copper smelting flue gas; particles; sulfation decomposition; copper arsenate; pyrite 1 Introduction Arsenic is a ubiquitous contaminant in the environment through geochemical migration andFormation of arsenic−coppercontaining particles and their 2018年11月1日 1 Introduction Zhijin phosphorus ore in Guizhou is an ultralarge moderate and lowgrade phosphorus mine containing rare earth 1, 2, 3 The explored reserve of the phosphorus mine is 1334 billion tons, and the rareearth oxide reserve is 1446 million tons Among them, heavy rareearth yttria accounts for 316%, which constitutes a large amount of rareearth oreMigration behavior, separation and recycling of rare earth In this work, the reaction mechanism of thermal ironore decomposition, ironore particle smelting reduction, and FeObearing slag smelting reduction on the three reactions were observed, providing a theoretical basis for how to select and optimize raw materials for the bath smelting reduction processStudy on the Bath Smelting Reduction Reaction and Mechanism of Iron Ore
.jpg)
Thermal Decomposition of Hematite Ore Fines in Air
2024年9月15日 As the grades of iron ore deteriorate, experimental and thermodynamic studies are conducted to understand the effect of gangue content on the thermal decomposition of Thermal decomposition of hematite plays an important role during pelletization and the iron finebased smelting processes such as HIsarna and flash shaft quieter smelting process Pretreatment of manganese ores prior to melting has also been suggested by other researchers [6,7] A successful heat treatment of manganese ores requires a comprehensive study of the ore behavior upon heating However, there is only a limited number of recent research [6,810] addressing the chemicalThermal upgrading of manganese ores prior to smelting2020年3月28日 Bauxite ore is the main raw material used to produce alumina (Al 2 O 3) which is the feedstock for aluminum productionThere are three main structural types of aluminum hydroxide minerals in bauxite: gibbsite (γAlO(OH) 3), boehmite (γAlO(OH)), and diaspore (αAlO(OH)) [1, 2]Apart from the aluminum minerals, basic components of bauxite also include On the Direct Reduction Phenomena of Bauxite Ore Using H2023年6月3日 Numerous catalysts have been studied and developed to catalyze the decomposition of methane and in this paper, an iron slab is selected as the catalyst to obtain stable Fe3C and C2 during the decomposition of methane We combine ReaxFF MD simulations and laboratory work to investigate methane decomposition and carburization of carbon atoms Investigation of methane decomposition and carburization with
.jpg)
Decomposition Characteristics of Iron Ore during Smelting
For the study of the thermal decomposition behavior of iron ore during smelting reduction, previous experimental methods included a thermogravimetric analysis (TGA) device, a heated horizontal furnace, and a hightemperature drop tube furnace, as shown in Figure 1 []This method is used to investigate the thermal decomposition temperature and properties of iron ores via Smelting, a method by which a metal we separate from its material, Metal extraction process in which ore is heated at a high temperature in an enclosed furnace (OH)2 This mineral undergoes thermal decomposition between 250° C and 350° C at 2CuO, CO2, and H2O Carbon dioxide and water release into the atmosphereSmelting Defintiion and Process and Roasting Smelting 2022年8月23日 Tleugabulov SM, Abikov SB, Altybaeva DK, Isupov YD, Tleugabulov BS (2015) Reductive smelting of iron ore Steel in Translation 45(5): 351355(PDF) An Overview of the ReductionSmelting Process of Iron 2023年3月22日 Internal cracking microstructure during the smelting reduction of #1 iron ore (a) Microstructure of cracks at 4 s with 100 μm scale; (b) Microstructure of cracks at 4 s with 10 μm scale; (c (PDF) Cracking and Microstructure Transition of Iron Ore

DesignYantai Jinpeng Mining Machinery, ore dressing process
Senior engineer of mineral separation, 35 years mineral experience, president of YANTAI ORIENTAL METALLURGY DESIGN AND RESEARCH INSTITUTE CO, LTD, he had designed more than thousands of mines, acted as the general designer of the biggest gold mine of Asia 8000t/d, he obtained the first prize of technology progressing and many awards as excellent 2023年10月15日 23 HIsmelt [] The process HIsmelt is also termed as ‘high intensity smelting’ In the process, liquid iron is produced straight from the iron ore The process (Fig 3) treats iron ore fines with minimum of pretreatment, providing a flexibility to quality of iron it can handleIron ore fines and noncoking coal with significant impurities could be fed to the processSmelting Reduction Technology – Current Status and Future 2016年5月1日 Geochemical partitioning of Tl in Pb–Zn ores and smelting wastes was investigated • Significant differences were shown in Tl contents and chemical fractionation • Over 100fold enrichment of Tl was found in electrostatic dust and acidic waste • Ore roasting played a key role in Tl transformation and mobilization •Thallium transformation and partitioning during Pb–Zn smelting tages make it difficult for lump iron ore to take advantage of its characteristics and therefore to replace sinter and pellets In the field of lump iron ore smelting, Wu19 studied the use of lump ore in blast furnace under laboratory conditions and concluded that there is a hightemperature interactivity between lump oreLump Iron Ore Preheating Treatment to Improve Softening
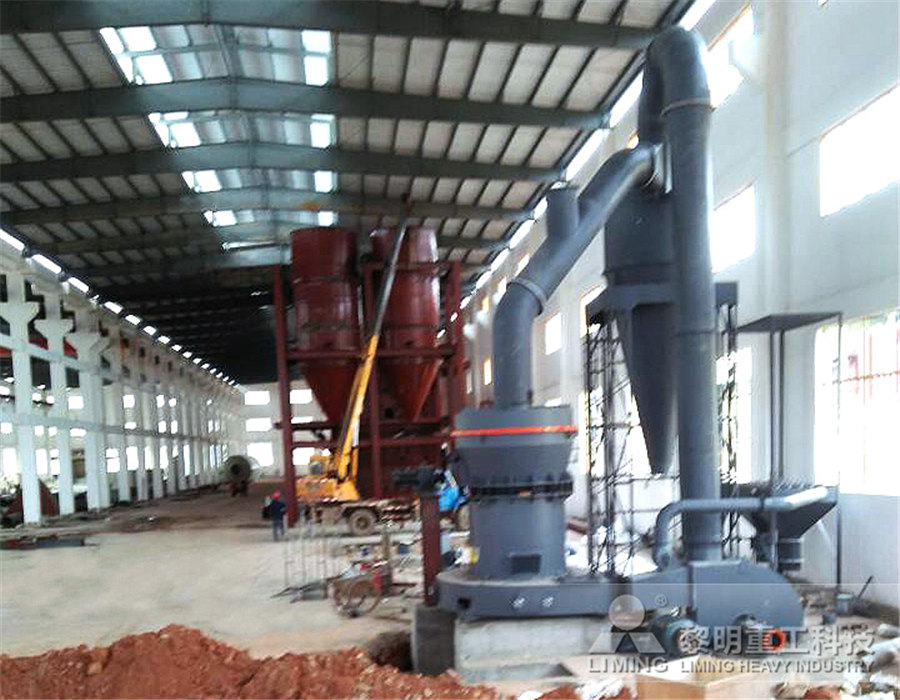
Decomposition of monazite in Bayan Obo rare earth ore by
2024年10月1日 In response to the above problems, researchers have proposed novel smelting processes, 14 including chlorination, HCl–AlCl 3, microwave roasting, and calcination 15 However, none have reached industrial production levels Traditionally, liquid alkali decomposition and Na 2 CO 3 roasting have been cleaner smelting processes for treating mixed rare earth hand, as that the smelting cyclone and SRV have a close contact and the reactions in the smelting cyclone would directly affect the operation parameters in the SRV Therefore, the kinetic study of the thermal decomposition of iron ore under the conditions of the smelting cyclone will be helpful to optimize the whole HIsarna process 2Thermal Decomposition Behaviour of Fine Iron Ore ParticlesMedia Attributions; Metal deposits are mined in a variety of different ways depending on their depth, shape, size and grade Relatively large deposits that are quite close to surface and somewhat regular in shape are mined using openpit mine methods (Figure 815 in Section 81)Creating a giant hole in the ground is generally cheaper than making an underground 82: Mining and Ore Processing Geosciences LibreTextsThe nonisothermal magnetization roasting process and isothermal magnetization roasting process of siderite ore were investigated using thermogravimetric (TG) analysis and a realtime infrared gas analyzer Xray diffraction (XRD) and scanning electron microscopy (SEM) with energy dispersive spectroscopy (EDS) were used to analyze the characteristics of samples Thermal Decomposition Kinetics of Siderite Ore during
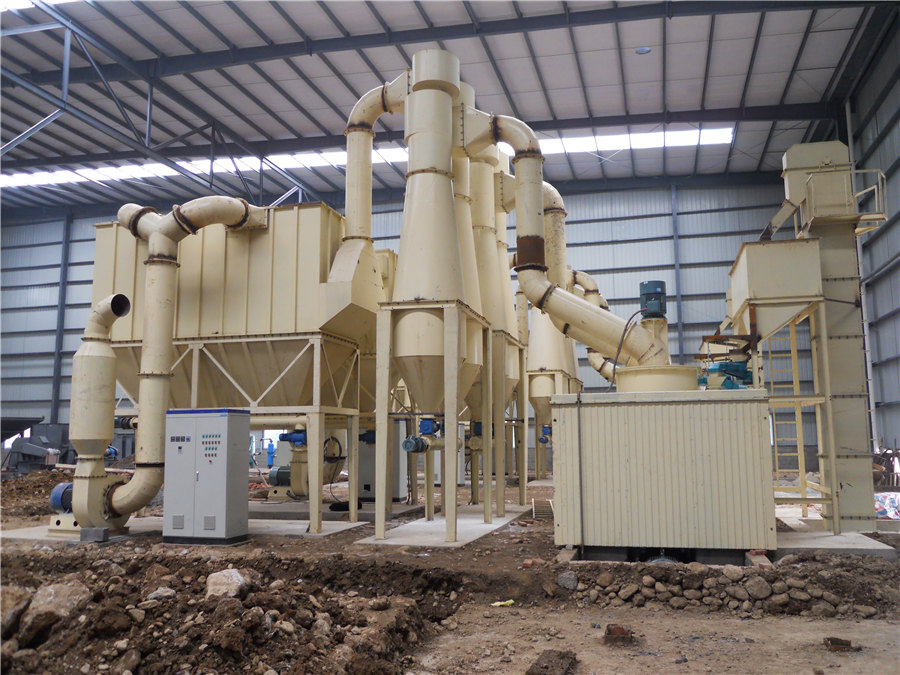
Thermal Decomposition Reaction Kinetics of Hematite Ore
2019年9月19日 In this work, the reaction mechanism of thermal ironore decomposition, ironore particle smelting reduction, and FeObearing slag smelting reduction on the three reactions were observed, 2024年1月4日 Separated preparation of prealloys and amorphous alloys results in severe solidification–remelting and beneficial element removal–readdition contradictions, which markedly increase energy consumption and emissions This study offered a novel strategy for the direct production of FePC amorphous soft magnetic alloys via smelting reduction of highphosphorus Clean production of Febased amorphous soft magnetic alloys via 2019年9月3日 and Kongoli conducted a similar pilot study in relation to the smelting of saprolitic Buruktal ores (Russia) In their work, briquetted and roasted ore was charged into the twozone V aniukov furnace(PDF) Nickel Laterite Smelting Processes and Some