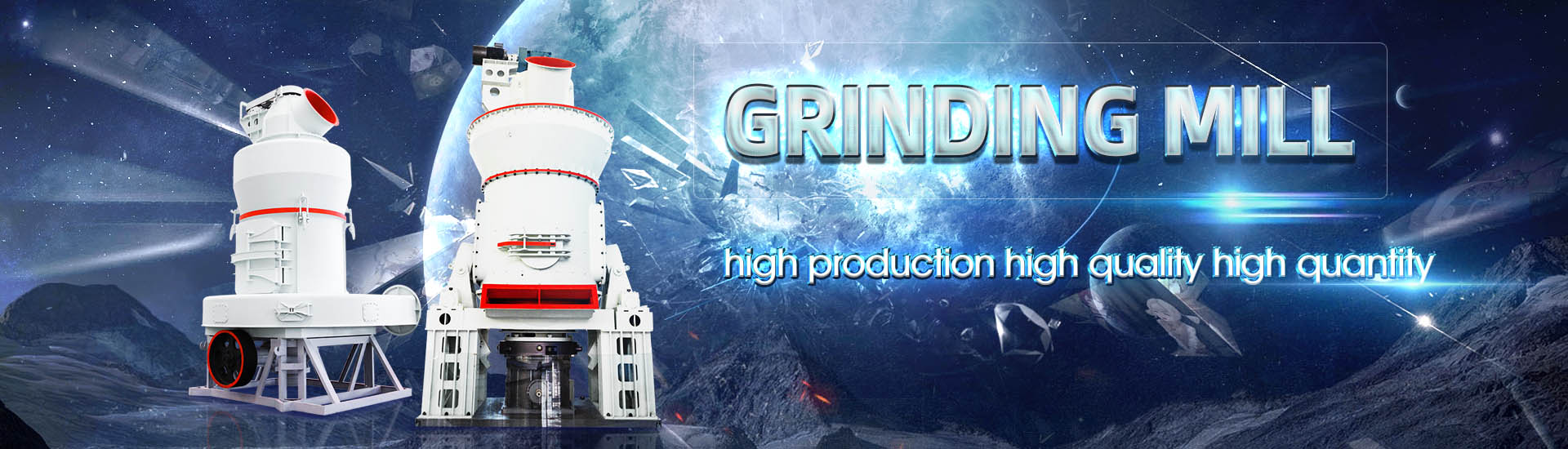
Coal grinding fineness
.jpg)
Improved Coal Fineness Improves Performance, Reduces Emissions
Since that time, pulverizer capacity has increased to meet the corresponding growth in unit sizes with incremental improvements in grinding efficiencies The pulverizer configuration usually found in most coalfired power generation plants is the vertical air swept design, although there are a number of ball tube pulverizers 展开2017年11月15日 A method for choosing the optimum fineness of coal in pulverisedfuel boilers is presented This method is based on economic criteria and takes into account variations of Optimisation of coal fineness in pulverisedfuel boilersting of the mill is determined by grinding The great variety of solid fuel properties, such as grindability, ash content, volatiles as well as the required product fineness, calls for a wide COAL GRINDING IMPS: more than meets the eye Gebr Pfeiffer2014年1月1日 Two mill systems are employed for most coal grinding applications in the cement industry These are, on the one hand, vertical roller mills (VRM) that have achieved a share of almost 90% and,(PDF) MPS mills for coal grinding ResearchGate
.jpg)
A Study on 500 MW Coal Fired Boiler Unit’s Bowl Mill Performance
major components of a coalfired thermal power station These are used for grinding the raw coal so that the pul are four major mechanisms that happen during the coal crushing in the mills 2017年11月15日 Achieving stable lowNO x combustion of coarse pulverized coal could improve the energy efficiency of the combustion system In this study, a pilotscale experiment on Optimisation of coal fineness in pulverisedfuel boilers2023年1月1日 Modern coalfired central generating plant makes use of a pulverized fuel (PF) firing system This technology is by far the most common for burning coal on a largescale Advances in pulverised fuel technology: understanding coal Grinding of coal up to μm size is indispensable to achieve its maximum calorific value and better combustion A systematic experiment, as well as modeling of grinding of Indian coal of size A statistical analysis and optimization of Indian coal grinding in a
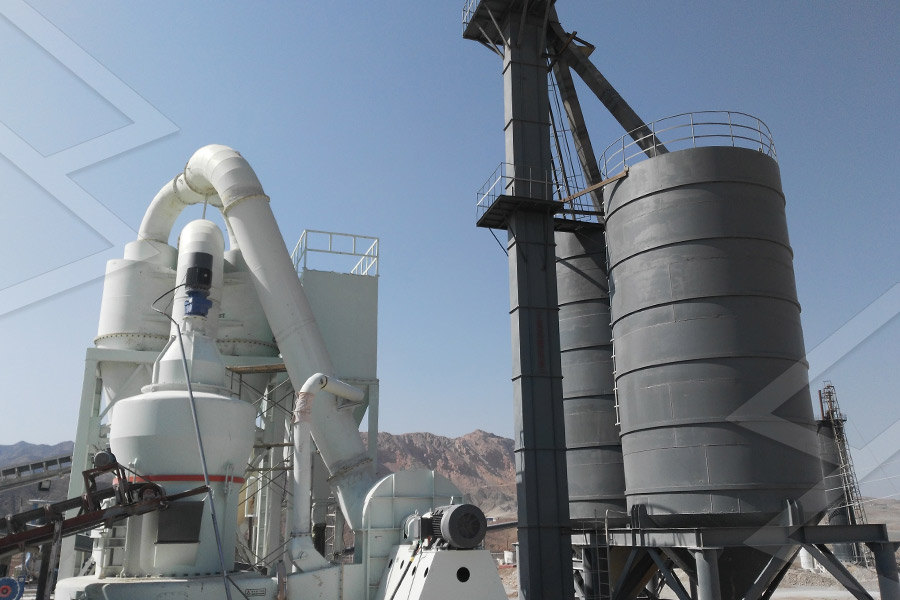
Evaluation of the Liberation Characteristic of Coarse Middling
2023年2月14日 In response to the shortages of coking coal, the grindingflotation separation process of coking middlings was proposed Researchers considered that moderate 2016年6月27日 Coal fineness is defined as the d 80 (80 % passing size) A quadratic model was developed to show the effect of parameters and their interaction with fineness of the product Grinding analysis of Indian coal using response surface methodologyfired thermal power station These are used for grinding the raw coal so that the pulverized product at the desired fineness can be fed directly to the furnace and fired for steam generation The major function of the Pulverizer is to grind the lumped coal A Study on 500 MW Coal Fired Boiler Unit’s Bowl Mill Performance ONLINE COAL FLOW MEASURING AND BALANCING (CONTROL) AND ONLINE COAL FINENESS MEASURING SYSTEM FOR COMBUSTION OPTIMISATION IN A THERMAL BOILER Suresh G Chandwani1, Dr Francesco Turoni2, Reinhardt Kock2, Dr Michael Haug2, Dr Michael Schreiber2 1NSGuzder Company Pty Ltd, Neville House, Currimbhoy Road, CPRI Online Coal Flow Balancing and Fineness Adjustment
.jpg)
Optimisation of coal fineness in pulverisedfuel boilers
Request PDF On Aug 1, 2017, Marek Pronobis and others published Optimisation of coal fineness in pulverisedfuel boilers Find, read and cite all the research you need on ResearchGate2017年11月15日 By the term “quality of pulverized coal” is understood its fineness (cumulative percentage retained R 009 and R 020) in conjunction with its homogeneity described by the uniformity (polydispersity) number nThe majority of hard coals combusted in the Polish power sector are bituminous coals of high volatile matter content in dry ash free state (V daf)Optimisation of coal fineness in pulverisedfuel boilers2023年2月14日 In this paper, the sizedensity distribution of coarse middling coking coal (CMCC) with different grinding fineness and flotation concentrates was investigated Then, the flotation behaviors and liberation characteristics of different sizedensity fractions in ground CMCC were analyzed, and the different sizedensity fractions were divided into five categories: most Evaluation of the Liberation Characteristic of Coarse Middling High turndown ratio – system allows safe, easy, instantaneous adjustment of capacity without affecting fineness, with a turndown ratio up to 5 to 1 Quiet, smooth operation – design insures no metaltometal contact between grinding rolls and ring, fuel grinds on fuel This results in smooth, vibrationfree operation with low noise levelsRaymond Bowl Mill designed and built for flexibility Qlar
.jpg)
Vertical Grinding Mill (Coal Pulverizer) Explained saVRee
Introduction This article concerns itself with vertical grinding mills used for coal pulverization only (coal pulverizers), although vertical grinding mills can and are used for other purposes The 3D model in the saVRee database represents a vertical grinding bowl millOther grinding mill types include the ball tube mill, hammer mill, ball and race mill, and , roll and ring mill2023年1月1日 Most coal mills are designed around achieving 100% throughput at 50–52 HGI and grinding lowHGI coals can lead to problems regarding their capacity to deliver suitable PF to maintain full boiler For an increase in fineness, there are combustion and heat transfer issues along with changes in such downstream issues as carbon in Advances in pulverised fuel technology: understanding coal grinding The coal properties such as volatile components, ash content, hardness, humidity and grinding fineness are the decisive factor for selecting the required mill Basically, coal pulverisers can be divided into three assembly groups, impact mills, gravityforce mills and external force millsCoal Mill an overview ScienceDirect Topics2016年6月27日 The present work discusses a systematic approach to model grinding parameters of coal in a ball mill A three level Box–Behnken design combined with response surface methodology using second order model was applied to the experiments done according to the model requirement Three parameters ball charge (numbers 10–20), coal content Grinding analysis of Indian coal using response surface methodology
.jpg)
Study on the influence mechanism of the grinding fineness on
2022年4月7日 Abstract In this paper, the influence mechanism of grinding fineness on the floatability of coking middings was analyzed by studying the flotation probability, cumulative flotation probability and water recovery in the flotation process The results indicated that in a moderateturbulence intensity flotation environment, the size, density and wettability of It pulverizes coal by applying hydraulicallyloaded grinding pressure through three grin ding rollers onto a rotating bed of coal Grinding pressure can be adjusted to account for variations in coal grindability and desired product fineness Raw coal is fed through a centrally located feed pipe to the center of the grinding tableA Comparison of Three Types of Coal Pulverizers Babcock Power2016年6月27日 Response surface of fineness of coal to the variation of number of balls and grinding time at average amount of feed of 150 gm for −165 + 4 mm size fraction Figures available via license Grinding analysis of Indian coal using response surface methodologyGrinding of coal up to µm size is indispensable to achieve its maximum calorific value and better combustion Moreover, wet grinding shows better results of fineness of coal Grindability of the coal was tested by standard Bond grindability test and A statistical analysis and optimization of Indian coal grinding in a
.jpg)
PowerGen 2008, Orlando, USA Online measurement of coal fineness
Online measurement of coal fineness and airfuel ratio inside the coal pipe Michael Schreiber, Michael Haug, Max Starke, Reinhardt Kock, Each coal has its distinctive grinding and sampling characteristics, and these change with production conditions Even when standard sampling methods are employed, The working characteristics of a laboratory ball drum mill during grinding of Karaganda coal products were studied in order to apply the results obtained to industrial installations The performed analysis shows that the most complicated and energyintensive stage of preparation of coal dust is the grinding of fuelOptimisation of coal fineness in pulverisedfuel boilers2022年2月24日 The fineness of grinding and specific surface area of the fi nal product were determined by the method of sieve analysis by sieving a sample of coal dust [35] using vibrating screensImproving the efficiency of the coal grinding process in ball drum 2024年11月20日 Key Features 1 High Efficiency: Capable of grinding coal into ultrafine powder with high throughput; 2 Adjustable Fineness: Produces powders with adjustable particle sizes, typically ranging from 60 to 400 mesh; 3 EnergySaving Design: Uses advanced technology to reduce energy consumption compared to traditional mills; 4 Robust Raymond Grinding Mill for Coal Powder Making Plant
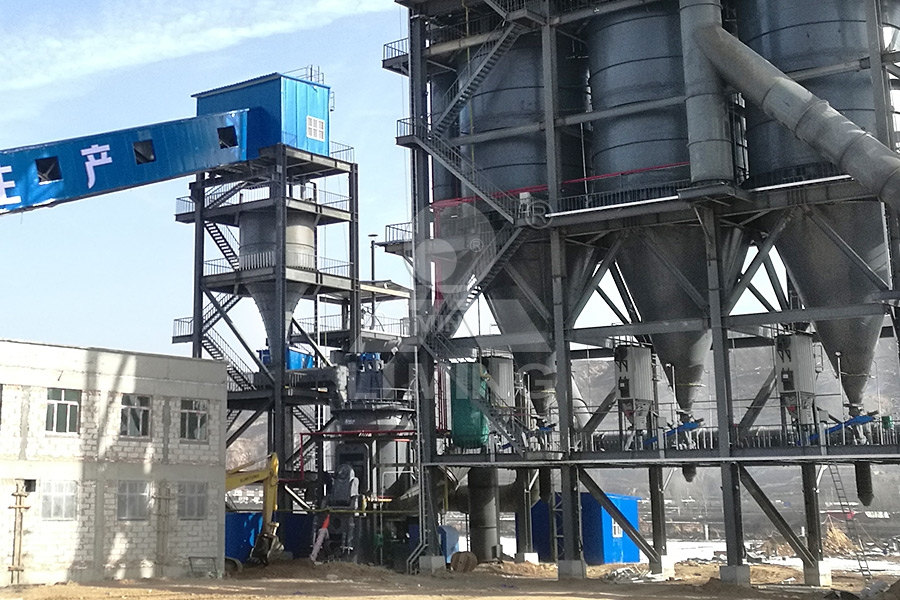
The Storm Approach to Coal Pulverizer Optimization
The point we are trying to make is this: coal pulverizer capacity is a specified fuel grinding capability or throughput at a certain HGI (coal grindability index) and also based on raw coal size, moisture and desired fineness level These factors are significant and must all be taken into2013年12月1日 Coal blending technology is commonly used in coalfired thermal power plant in recent years to ease cost pressures But thermal power plants still use empirical formula to determine the economic fineness of pulverized coal This approach cannot change economic fineness of pulverized coal based on the proportion of blending coal timely and accurately, A New Method for Determining Pulverized Coal Economic Fineness2022年12月1日 The test material was plates made of high manganese cast steel that acts as a beater on a MWk 12 (FPM SA Mikołów, Poland) beater mill for coal grinding (Fig 1)The diameter of the beater mill rotor was 2186 mm, 10 beaters were installedThe wear mechanism of mill beaters for coal grinding madeup 2 Reprint from / Sonder druck aus ZKG 3 2014 zkg GEBR PFEIFFER SE MPS mills for coal grinding TEXT Dr Caroline Woywadt, Head of Process Engineering, GebrPfeiffer SE, Kaiserslautern/Germany In most areas of industrial grinding of bulk solids material, vertical roller mills (VRM) haveReprint from ZKG 3 Gebr Pfeiffer
.jpg)
Optimisation of coal fineness in pulverisedfuel boilers
2017年11月15日 Semantic Scholar extracted view of "Optimisation of coal fineness in pulverisedfuel boilers" by M Pronobis et al Skip to search form Skip to main content This paper deals with the system of automated control and optimization of coal grinding by means of ball mills at thermoelectric power stations The system provides the fineness is reduced from about 75% passing 200 mesh to 45% passing 200 mesh, as much as 30% more coal throughput can be pushed through the pulverizers The previous example is often inadvertently done by increasing primary airflows or opening classifier blades up to increase the coal flow to the furnace by sacrificing coal finenessPulverizer Capacity is not simply “tons throughput per hour!”2022年2月28日 Since the grinding specific energy is a function of feed rate and related to the product fineness, a direct correlation between product fineness and feed rate can be observed When the feed rate decreases, an increase in the product’s surface area occurs, and therefore, an inverse relationship between feed rate and product size can be defined [ 115 , 116 ]Grinding SpringerLinkEffect of Fineness Fineness of pulverised coal More the fineness less is the capacity 70% through 200 mesh Number of opening per linear inch 50 mesh sieve will have 2500 openings per square inch Volatile content below 16% would required higher Pulverizer Plant OM Aspects
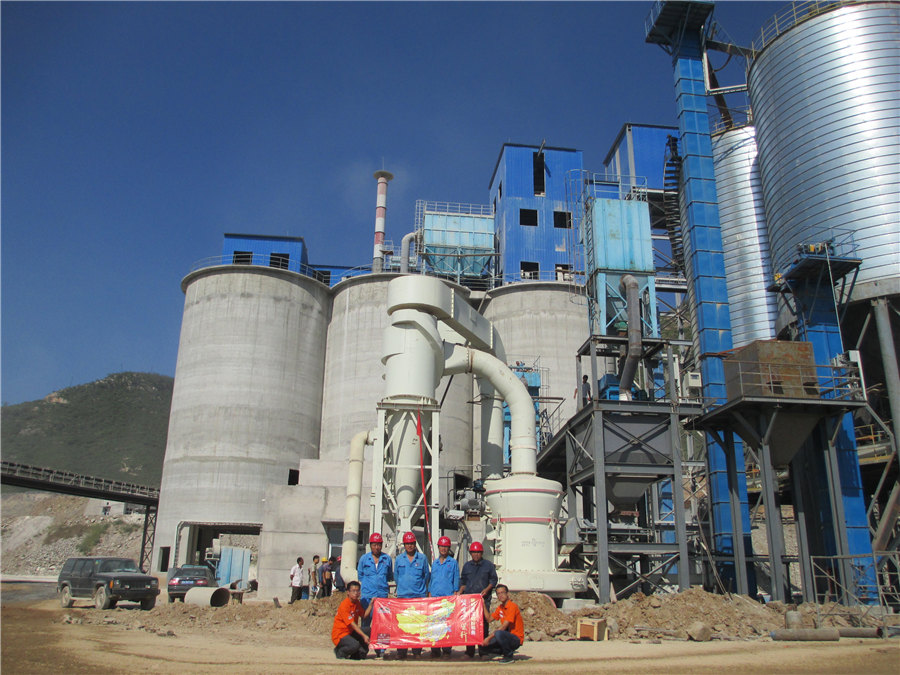
A unified thermomechanical model for coal mill operation
2015年11月1日 In this zone, coal entrainment and drying is taken into account Mixed air entrains the coal from grinding zone and dries the coal First stage classification is considered here, fineness, coal level in the mill together with size information can provide indication of the mill condition/faults inside the millareas of the burner coal pipes and coal nozzles (Figure 8) Step 4 Properly maintain the classifier Once the grinding zone is blueprinted and put in firstclass condition, the next component to examine is the classifier The best furnace combustion performance is governed by uniform coal combustion by the burners and satisfactory coal fineness“Blueprint” Your Pulverizer for Improved Performancespindle coal pulverising mill’s performance to facilitate optimal plant performance Plant design and mill’s acceptance test data was analysed to understand the design and subsequent changes over the years of the mill’s operation The mill outputs, pulverised coal fineness andPerformance optimisation of vertical spindle coal pulverisers2009年2月1日 The effects of roasting, mass ratio of H2SO4 to stone coal, leaching temperature, liquidtosolid ratio, grinding fineness of stone coal, and twostage countercurrent leaching on the vanadium Leaching of vanadium from stone coal with sulfuric
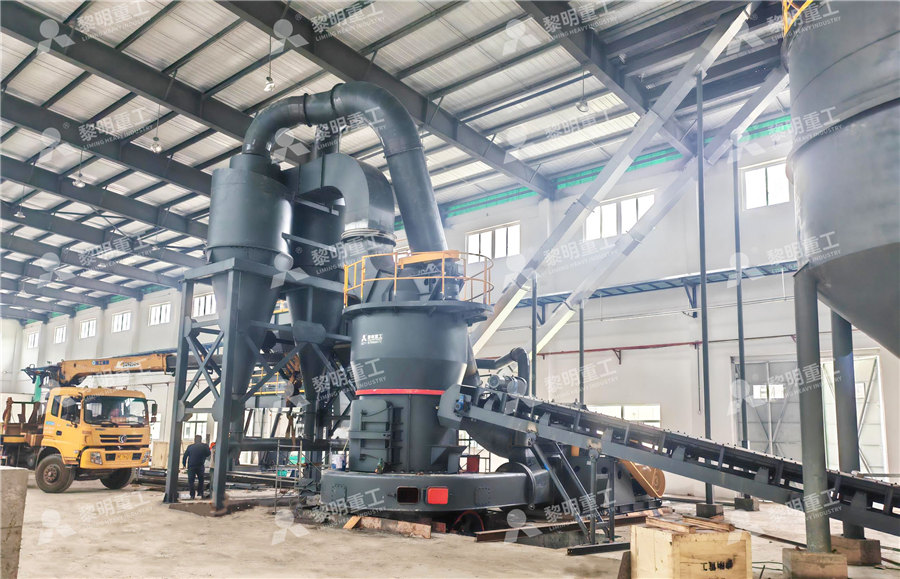
CHINA COAL GRINDER SUPPLIERS GRINGDING MILL FINENESS
Large pieces of coal are crushed by the crusher to the fineness (15mm50mm) that can enter the mill 2 Drying and grinding A The crushed coal material with relatively low moisture content is sent to the storage hopper by the elevator, and then sent to the grinding chamber of the mill evenly and quantitatively by the feeder for grinding2016年4月5日 In PFboilers, coal is pulverised in a mill (or pulveriser) before being entrained by primary combustion air to burners, to form a high temperature flame in the furnace of the boiler (1000–1600 °C) [2]The fineness of the coal powder, as well as the uniformity of the coal flow sent to each burner fed by the same mill, are crucial parameters to achieve an effective combustion Online monitoring of coal particle size and flow distribution in coal 2019年5月1日 This study investigated ultrafine coal grinding performance of four low to moderatecost grinding media in a laboratory stirred mill Kinetic grinding tests showed that silica beads generated the finest product size with a P 80 of 59 μm from a feed size of 244 μm while having a specific energy (SE) input of 309 kWh/tonNew method for increase in product fineness in stirred millsfor coal grinding installations And thanks to our continuous refinement of the ATOX coal mill over the years, today’s leading airswept vertical roller mill is the compact ATOX Offering high reliability, low installation costs and a wide range of sizes, the ATOX grinds and dries all types of coal – while providing excellentATOX COAL MILL FLSmidth Cement
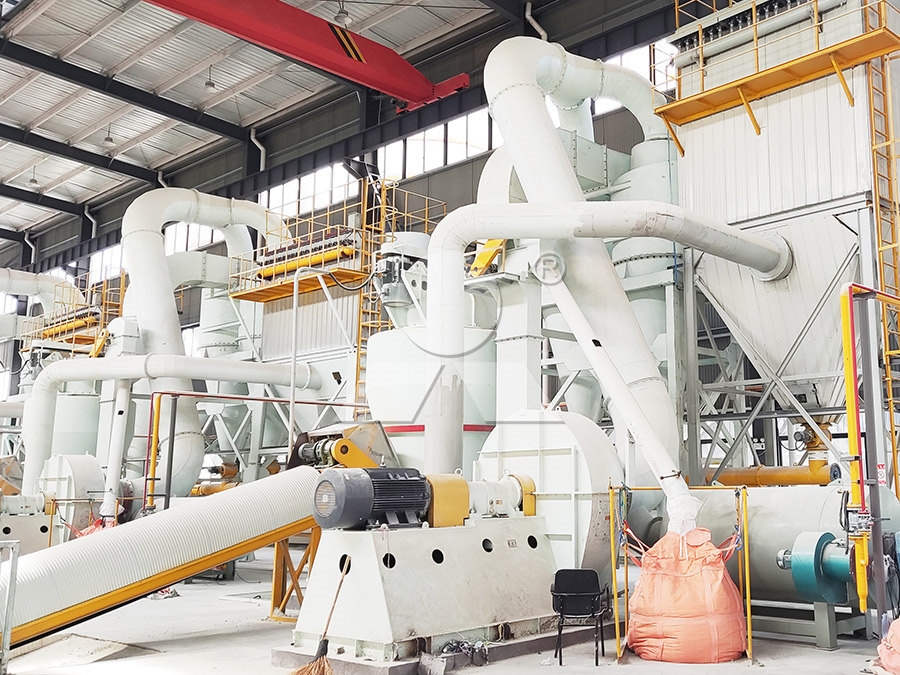
Response surface of fineness of coal to the variation of grinding
Download scientific diagram Response surface of fineness of coal to the variation of grinding time and amount of feed at average number of balls of 15 for −165 + 4 mm size fraction from 2019年2月28日 The grinding process is necessary to convert original coal bottom ash (CBA) into a powder form The aim of this study is to evaluate the grinding process effects on physical properties of CBA, it Effects of Grinding Process on the Properties of the Coal Bottom 2022年4月7日 In this paper, the sizedensity distribution of coarse middling coking coal (CMCC) with different grinding fineness and flotation concentrates was investigatedStudy on the influence mechanism of the grinding fineness on