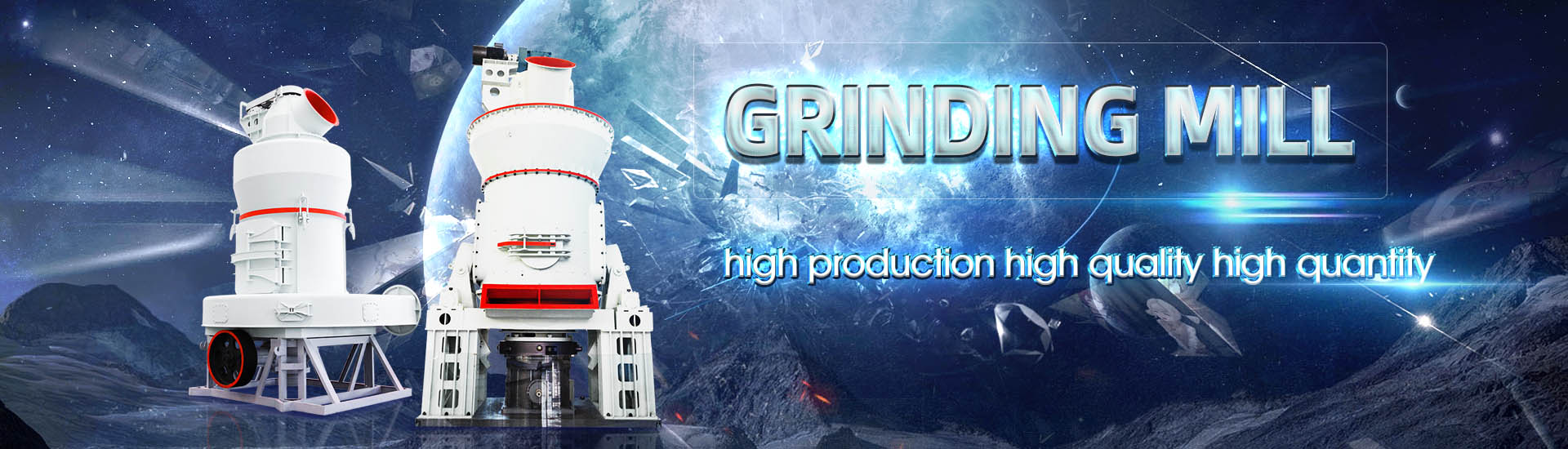
Air sweep grinding process
.jpg)
What is an Air Swept Mill? Prater
Air swept mills finely grind the material with or without screens, typically producing diverse particle sizes during processing Also often referred to as impact mills, they’re ideal for pulverizing a wide array of materials up to 50 microns2017年5月25日 In an airswept mill, the body of which does not differ significantly in general design from a trunnion overflow mill, a powerful stream of air is passed through the mill and Air Swept Mill 911MetallurgistBradley Airswept Mills combine the fine grinding action of a pendulum roller mill with air stream classifying and fluid bed drying capabilities to produce precisely sized particles to meet exact Airswept Roller Mills Bradley Pulverizer Company1996年3月1日 Fine grinding in a ball mill working in closed circuit with a forced vortex air classifier has been investigated in continuous laboratory scale The ball mill was tested as a Ultrafine grinding in an airswept ball mill circuit
.jpg)
Air Classifying Mill
The Mikro ACM® Air Classifying Mill is an air swept mechanical impact mill with a dynamic air classifier designed to grind an extensive range of materials down to a D97 of 20 microns The The CMS Air Swept Classifier Mill System combines dynamicimpact grinding and particle size classification in a single continuous process Independent drives for the Impact Rotor and Classifier Wheel allow the system operator to Air Swept Classifier Mill System How it Works, Bradley Airswept Mills combine the fine grinding action of a pendulum roller mill with air stream classifying and fluid bed drying capabilities to produce precisely sizedAIRSWEPT PENDULUM MILL SYSTEM Bradley Pulverizer2015年4月1日 In this study, production capacity of a fully airswept dry grinding raw meal ball mill circuit was evaluated by modelling the mill using the perfect mixing modelling approach Optimization of a fully airswept dry grinding cement raw meal
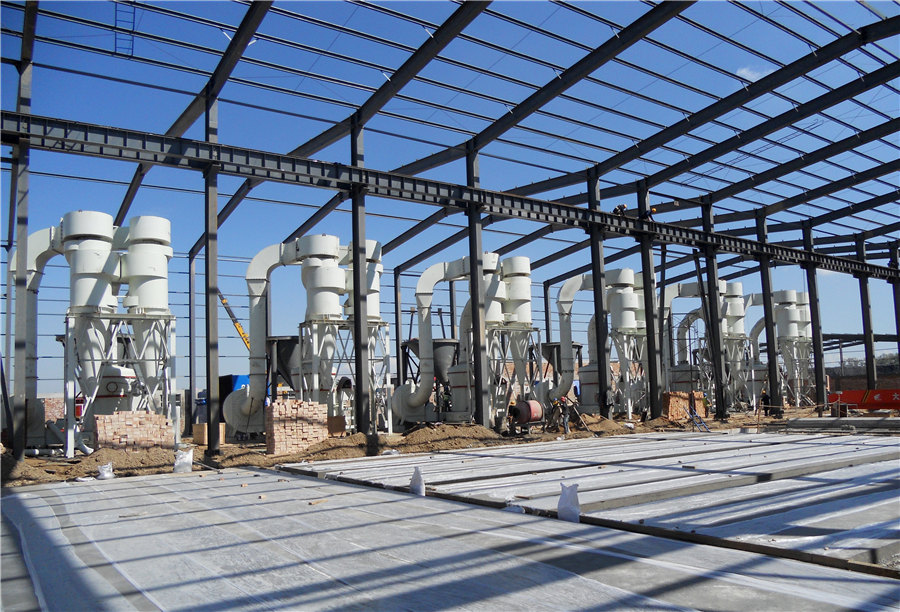
Ultrafine grinding in an airswept ball mill circuit ResearchGate
1996年3月1日 The grinding process of an airswept tube mill can be modelled adequately using the selection and breakage functions approach to modelling comminution2005年2月20日 This paper is concerned with the model of a fully air swept ball mill operating in a raw material grinding circuit For simplicity, the approach assumes that different components in Modeling and simulation of a fully air swept ball mill in a raw Surface grinding is a precision machining process used to produce smooth and flat surfaces on a variety of materials, including metals, plastics, and ceramics The process involves using a grinding wheel, which is made up of abrasive particles, to remove material from the surface of a workpiece until it is smooth and flatSurface Grinding EngineeringTechnologyImpactful Grinding Chamber: Materials are finely broken down by strategically positioned hammers on a rotating shaft Adjustable Wizards: Streamlined feeding process for enhanced efficiency HighEfficiency Bag Filter: Fully Air Swept Mills Rieco
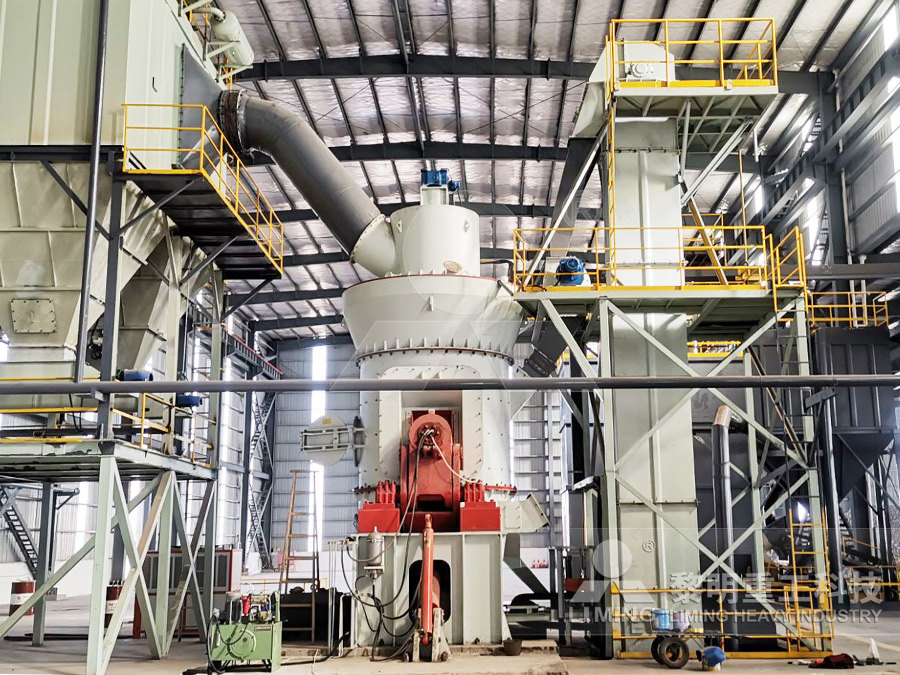
PROCESS CONTROL FOR CEMENT GRINDING IN VERTICAL
The power ingesting of a grinding process is 5060% in the cement production power consumption The Vertical Roller Mill (VRM) reduces the power consumption for cement grinding approximately 3040% associated with other grinding mills The process variables in cement grinding process using VRM are strongly nonlinear and having large timeDuring a machining process with a trackbound cutting edge engagement, the cutting edge of the grain penetrates the workpiece upon a flat path and, after a phase of elastic deformation, triggers plastic flow of the workpiece material (Fig 3)Due to the shape of the cutting edge, the angle between the cutting edge contour and the workpiece surface is very small at the beginning of Grinding Process SpringerLinkThe system combines vacuum action with our Air Knife’s blowoff forces to quickly remove surface water, starch, and scraps from justwashed potato slices, fruits, vegetables, and other products before frying or freezingAirSweep® Water Removal System Heat and Control2022年6月13日 Yes AirSweep can be installed in any vessel or area where material has a tendency to hang up Aside from silos, hoppers, and other material storage containers, it can be placed in gravity chutes, fine grinding mills, extruders, pneumatic convey lines, cyclones, pipes (including elbows and bends), cyclones, and more AirSweep can also be AirSweep Installation FAQs Control Concepts, Inc
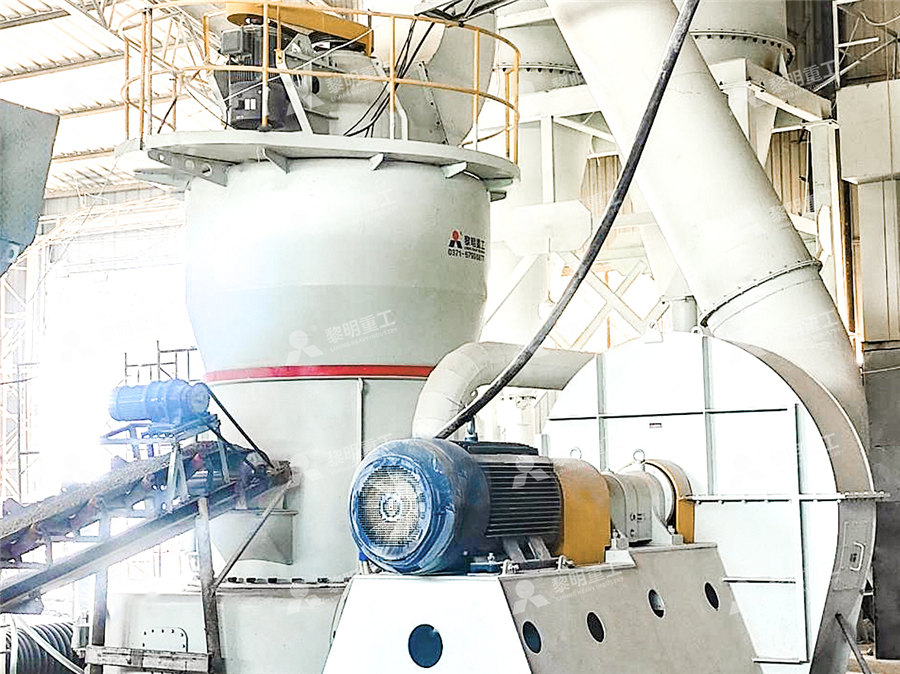
The Process Optimization Analysis of CBN Abrasive CuSnTi
2024年9月3日 Ultraprecision machining has higher requirements for the performance of abrasive tools, but the traditional grinding wheel has some problems such as irregular grain arrangement, limited chip space, and high grinding temperature Therefore, a structured grinding wheel suitable for ultraprecision machining is proposed In this study, the laser cladding 2022年6月24日 Grinding is a manufacturing process which significantly contributes in producing high precision and durable components required in numerous applications such as aerospace, defence and automobiles This review article is focused to uncover history, witness the present and predict the future of the grinding processA comprehensive review on the grinding process: Advancements For customers with an existing Hosokawa ACM, the process of retrofitting an E3 Beater is easy, involving minimal downtime and a simple replacement of the current grinding disc, with no other modifications required Customers choosing to invest in upgrading to the enhanced grinding disc will see a return on investment in less than a yearACM Air Classifier Mill Hosokawa Micron Ltd2023年3月25日 Unfortunately, grinding and polishing materials like concrete can create a lot of dust It is important to know how to clean concrete dust after grinding Although some jobs require more finishing than others, the cleanup process is essential for How to Clean Concrete Dust After Grinding 6 Useful Guide
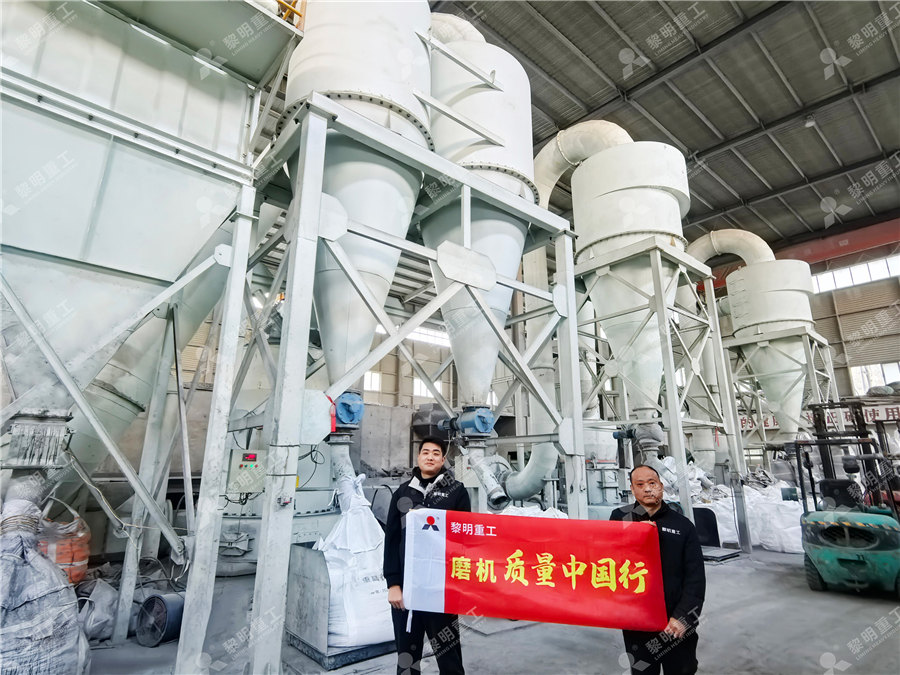
Grinding in Engineering:Definition,Process,and Applications
This article provides an overview of grinding in engineering, highlighting its role as an abrasive machining process essential for producing highquality, precision components in industries like aerospace, automotive, and electronics It discusses the various types of grinding (surface, cylindrical, centerless, etc), the equipment used (grinding machines, abrasive wheels, 2021年2月27日 The abundant use of cutting fluids in surface grinding process and the corresponding costs and energy consumption have been a major sustainability concern This paper identified the optimum depth of cut for surface grinding under controlled grinding parameters using compressed air cooling technique and dry cutting The surface morphology Evaluation of surface grinding of AISI 304 stainless steel using dry 2024年1月12日 The machine, grinding, and workpiece are all in an elastic floating working state when grinding since the process uses extremely fine micronized abrasives The convex spots of the processed surface are What Is Grinding Process Benchmark AbrasivesGrinding is the common collective name for machining processes that utilize hard, abrasive particles as the cutting medium The grinding process of shaping materials is probably the oldest in existence, dating from the time prehistoric humans found that they could sharpen their tools by rubbing them against gritty rocksGrinding Processes SpringerLink
.jpg)
Grinding and Abrasive Machining – EngineeringTechnology
The process involves using a grinding wheel, which is made up of abrasive particles, to remove material from the surface of a workpiece until it is smooth and flat The surface Handheld Grinding Handheld grinding refers to the use of handheld power tools for grinding, sanding, honing, and polishing various materialsHow the Air Swept Pulverizer Works The infeed material is fed into the air stream at the mill inlet (1) in a consistent metered fashion The beater plates (2) impact and reduce the size of the largest particles and distribute the material around the periphery of the grinding zone where product is ground against the liner (3) by the hammers (4) which are mounted on the beater Air Swept Pulverizers Carter Day International, Inc2011年7月1日 Fine grinding and dispersing, such as grinding in stirred media mills, gains importance in several industrial processes Solid materials processing is frequently subjected to dynamic changes Grinding in an air classifier mill Part I: Characterisation of the 2013年1月1日 PDF Principles of Modern Grinding Technology explains the principles that led to rapid improvements in modern grinding technology over recent decades Find, read and cite all the research Principles of Modern Grinding Technology ResearchGate
.jpg)
Air Classifying Mill
the mill along with the process air Ideally, material is fed at a constant rate via a volumetric or gravimetric feeding device After passing through the feed inlet, material enters the grinding zone At this point, material comes in contact with the face of the rotating hammers, where impact takes place and the material isgrinding mills The process variables in cement grinding process using VRM are strongly nonlinear and having large time delay characteristics also dynamics changes within 24 minutes The fast dynamics necessitate closer attention to the PROCESS CONTROL FOR CEMENT GRINDING IN VERTICAL AirSweep provides ondemand flow of even the toughest materials It eliminates bridging, ratholing, arching, and buildup in any vessel or chute nozzle directs highpressure, highvolume, 360degree bursts of compressed air or inert gas along the inside walls of process equipment or vesselsAirSweep AirSweep AsiaOne is "fixed abrasive processing" that uses tools with fixed abrasives such as belt grinding, tape grinding, and sandpaper, as well as polishing and lapping The second is "free abrasive processing" in which the abrasive is mixed with a What is Blasting? Explain the types and differences of
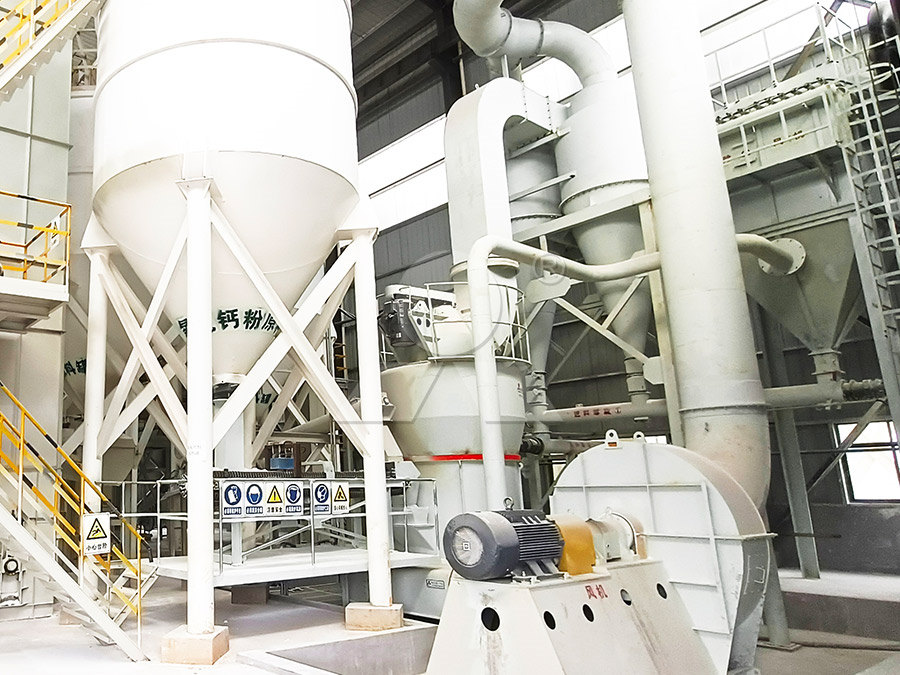
Optimizing AirClassifying Mills for Best Results
2022年3月22日 The larger particles, as determined by the application, are returned either by gravity or process air back to the grinding chamber for further reduction Adjust Mill Speed and Feed Rate for Optimal Results The mill 2021年5月5日 It is also known as the Abrasive Grinding Machining Process Why Abrasive Grinding Machining Process? Because the abrasives are placed on the surface to do the finishing process with much more accuracy The grinding machine is widely used to finish the workpiece Do you know why? Because the work removal rate is low between 025 to 05 mmGrinding Machine: Definition, Parts, Working Principle, Operation 2024年9月27日 Grinding Working Process Grinding is a precise mechanical machining process that removes material from a workpiece surface using a rotating grinding wheel Composed of abrasive particles, the wheel acts like numerous sharp cutting tools, scraping away layers of material to achieve desired shapes and surface finishesWhat is Grinding: Definition, Types, Uses, and Working ProcessSeperatorsdocx Free download as Word Doc (doc / docx), PDF File (pdf), Text File (txt) or read online for free This document discusses cement manufacturing and air separators It describes different types of separators including first, second, and third generation separators as well as static grit separators It provides details on the components and operation of static grit Air Separators: Introduction To Cement Manufacturing
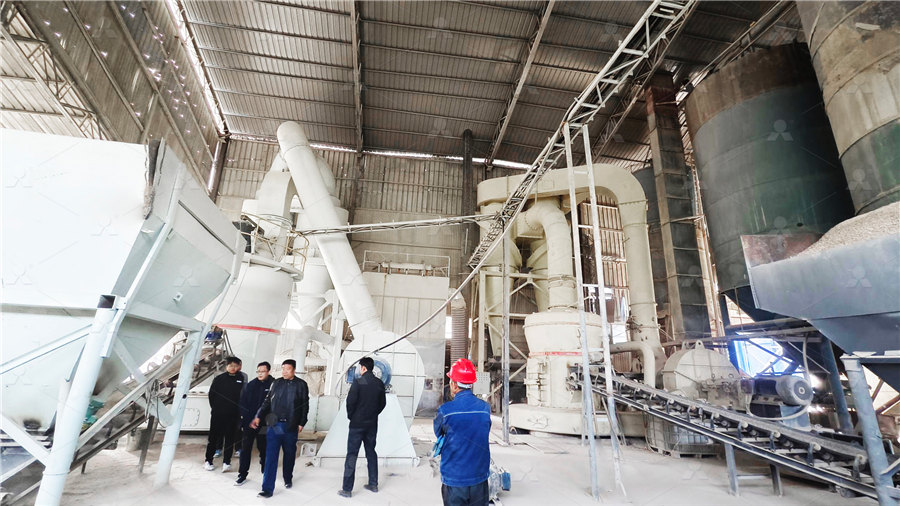
What is Wet Grinding Process Wet Ball Milling Method and
Explore the wet grinding process, its methods, and technologies in various industries, including pharmaceuticals, mining, and food processing Read in Allwin's blogGrinding is an abrasive machining process that uses a grinding wheel or abrasive belt as the cutting tool It is commonly used to remove material from a workpiece, to produce a smooth finish on the surface of the workpiece, or to remove burrs from the surfaceWhat is Grinding? – Working Principles, Applications Use of The grinding process has the least material removal rate among other machining processes because of the following reasons Size effect: As above discussed the machining is done by the abrasive action of grinding wheel that’s why a large portion of the abrasive will be embedded inside the wheel and a small portion of abrasive will be allowed to interact with them , Grinding Machining Process : Complete Notes Mech4studyGrinding in the cement industry is a critical process as it is the last step before the finished product is obtained There are other subprocesses involved in grinding, such as material transport or separation, but this work focuses on the actual grinding process that takes place within the VRMParámetros para el Proceso de Molienda en Molinos Verticales
.jpg)
Grinding Parameters SpringerLink
2019年1月1日 Further parameters relevant for grinding processes are the width of the grinding wheel b s, the width of the workpiece b w, and the diameter of the grinding wheel d s as well as for cylindrical grinding the diameter of the But what is the AirSweep® system, and is it the best solution for your particular process? This video gives you the big picture Find out: How AirSweep works, and how it compares to other material activation devices like fluidizers, air AirSweep Material Activation System: A Quick Look2021年7月3日 Grinding process control balances these three interactions to achieve the desired parameters These interactions feed into three major commercial grinding processes: rough grinding, precision grinding and ultra Machining 101: What is Grinding? Modern Machine 2022年6月29日 DOI: 101177/ Corpus ID: ; Evaluation of the grinding process utilizing an auxiliary compressed air jet on cleaning the grinding wheel surface @article{HatamiFarzaneh2022EvaluationOT, title={Evaluation of the grinding process utilizing an auxiliary compressed air jet on cleaning the grinding wheel surface}, author={Omid Hatami Evaluation of the grinding process utilizing an auxiliary
.jpg)
Evaluation of surface grinding of AISI 304 stainless steel using dry
rial removal process is surface grinding Surface grinding is a very vital machining process Surface grinding is carried out on a workpiece to create good surface nish [] 3 Besides surface grinding, there are also dierent types of grinding These include cylindrical grinding, creepfeed grinding and centreless grinding Grinding is used2022年6月29日 Grinding process with modified wheel led to an increase the bubble nucleation site formation and departure frequency in surface channels For a more detailed study, Evaluation of the grinding process utilizing an auxiliary 2024年4月19日 These will protect you from flying debris, sparks, noise, and harmful dust particles generated during the grinding process Step 3: Check the Grinding Wheel Inspect the grinding wheel to ensure it is in good condition Look for any cracks, chips, or other damages that might cause the wheel to break during operationThe Grind: Understanding The Processes Of Grinding MachinesAquí nos gustaría mostrarte una descripción, pero el sitio web que estás mirando no lo permiteClassifier Milling Systems Milling System Manufacturer
.jpg)
Optimization of internal plunge grinding using collaboration of the air
2019年8月6日 As one of the most critical machining operations, plunge grinding is used as a highproductivity finishing technology In the process of a plunge grinding, the highspeed rotating wheel moves only along the radial direction to the lowspeed workpiece []And the surface roughness and form accuracy of workpiece are directly affected by the infeed speed of wheel 2019年1月22日 Whether you are grinding or honing the ID, the tube must be held That means both of these internal grinding processes are limited in how small the diameter of the tube can be Grinding may also be used on the cavities in cast parts, to eliminate the porous surface and get the desired final shapeSpecialized Methods of Internal Grinding Metal Cutting