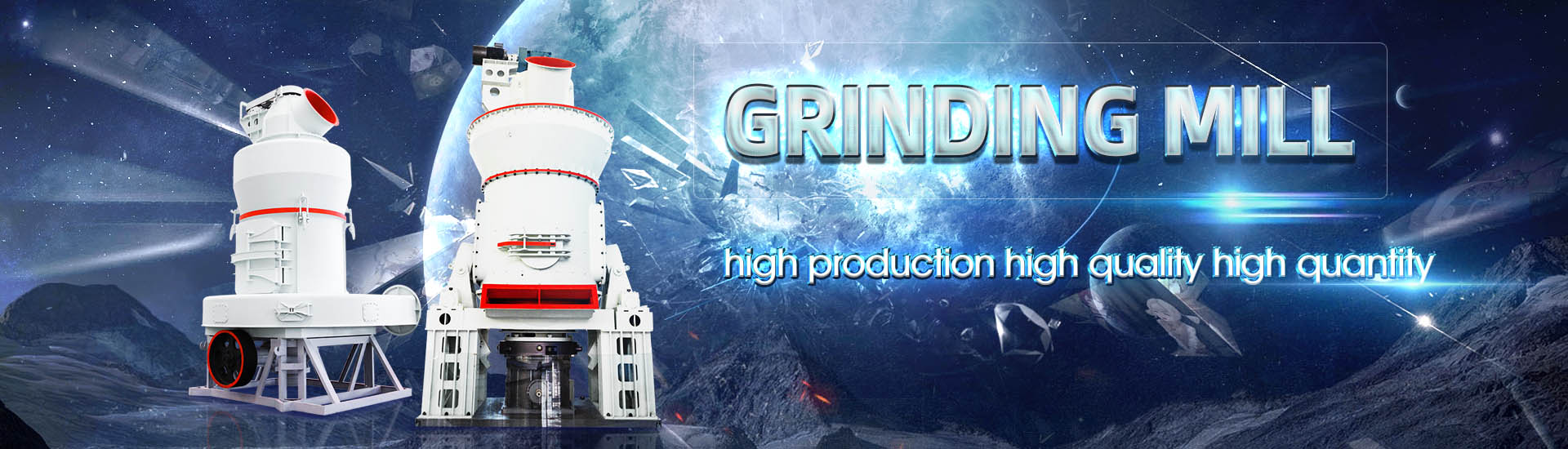
Power plant primary ore grinding mill model
.jpg)
The Evolution of Grinding Mill Power Models Mining, Metallurgy
2019年1月30日 Mill power models have been used in a variety of ways in industrial practice since power directly equates to throughput and fineness of ground product We first start with 1992年1月1日 The JKMRC mill filling soft sensor (JK MillFIT) utilises mill power draw and mill load (bearing pressure or load cell), which are measured in real time, and integrates models developed(PDF) Prediction of grindingmill power ResearchGateAs a critical part of the comminution process, autogenous grinding (AG) or semiautogenous grinding (SAG) mills are often used for primary grinding However, the breakage mechanism of Dynamic Modeling and Simulation of SAG Mill Circuits with2023年7月1日 This study aimed at investigating the grinding and classification behaviors of elements found in the copper ore grinding circuit Such expertise is beneficial for a real plant to Element based ball mill and hydrocyclone modelling for a copper
.jpg)
Modeling of Bauxite Ore Wet Milling for the Improvement of
2021年9月5日 The present study through batch laboratory experiments aims to model grinding of bauxite ore and identify the optimum material filling volume in a ball mill Modeling involves We first start with HoggFuerstenau Power Model and show how this model successfully predicted the power draw of many grinding mills in several mining operations Then, we show how this The Evolution of Grinding Mill Power ModelsIn overall terms, electricity accounts for 38% of Barrick’s total energy and the primary ore grinding consumes about 55% of the electricity and is associated with million tonnes per year of 17 IMPROVING ENERGY EFFICIENCY IN BARRICK GRINDING CIRCUITSA hybrid nonlinear model predictive controller (HNMPC) is developed for a runofmine ore grinding mill circuit A continuoustime grinding mill circuit model is presented with a Hybrid nonlinear model predictive control of a runofmine ore
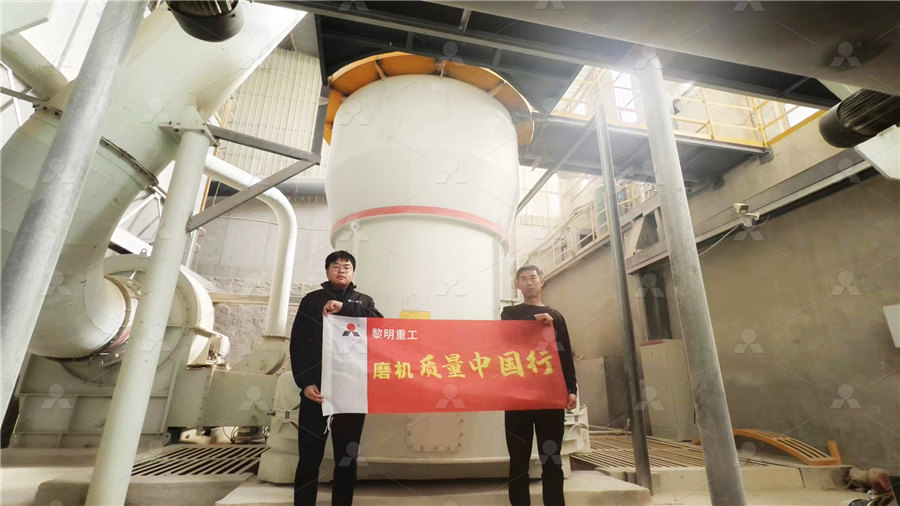
Analysis and validation of a runofmine ore grinding mill circuit
A simple and novel nonlinear model of a runofmine ore grinding mill circuit, developed for process control and estimation purposes, is validated The model makes use of the minimum 1 Population balance model approach to ball mill optimization in iron ore grinding Patricia M C Faria1,2, Luís Marcelo Tavares2 and Raj K Rajamani3 1 Vale SA, Brazil 2 Department of Population balance model approach to ball mill optimization in iron ore A crushing plant delivered ore to a wet grinding mill for further size reduction The size of crushed ore (F 80) was 40 mm and the SG 28 t/m 3 The work index of the ore was determined as 122 kWh/t A wet ball mill 1 m × 1 m was chosen to grind the ore down to 200 micronsGrinding Mill an overview ScienceDirect Topics2003年1月31日 They observed that the mill weight and the power draw decreases by increasing the top size of the feed ore Hahne et al (2003) reported that a significant loss of grinding action within the AG Ore characterisation for––and simulation of––primary autogenous
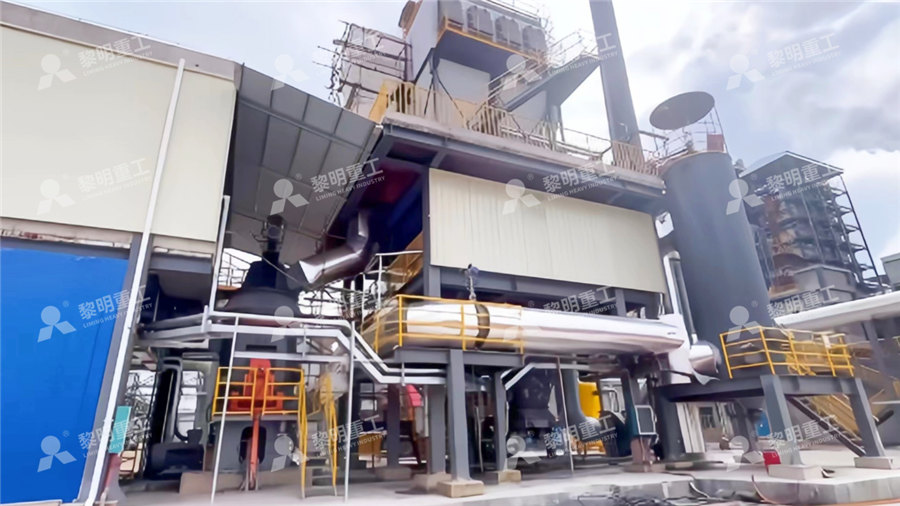
Hybrid nonlinear model predictive control of a runofmine ore
The mill is the most power intensive element in a grinding mill circuit and the power draw of the mill motor is represented by P mill [4] The slurry mixture of ground ore and water in the mill is discharged into the sump through an enddischarge screen that limits the particle size of the discharged slurry The level of the slurry in the 42017年2月20日 When choosing primary autogenous grinding, run of mine ore up to 200300 mm in size is fed to the mill The pebble weight is 525% of the total feed to the plant, Grinding Mill Power As may be seen on the figure opposite, Grinding Mill Design Ball Mill Manufacturer 911MetallurgistThe mill is the most power intensive element in a grinding mill circuit and the power draw of the mill motor is represented by P mill [4] The slurry mixture of ground ore and water in the mill is discharged into the sump through an enddischarge screen that limits the particle size of the discharged slurry The level of the slurry in the 4Hybrid nonlinear model predictive control of a runofmine ore which use both ore and steel balls as grinding media (Wei and Craig, 2009b) In the case of a ball mill the ore is crushed before it enters the mill, whereas a SAG mill receives runofmine (ROM) ore directly (Stanley, 1987) A SAG mill in a singlestage closed circuit con guration, as shown in Fig 1, is considered for this study A descriptionAnalysis and validation of a runofmine ore grinding mill circuit
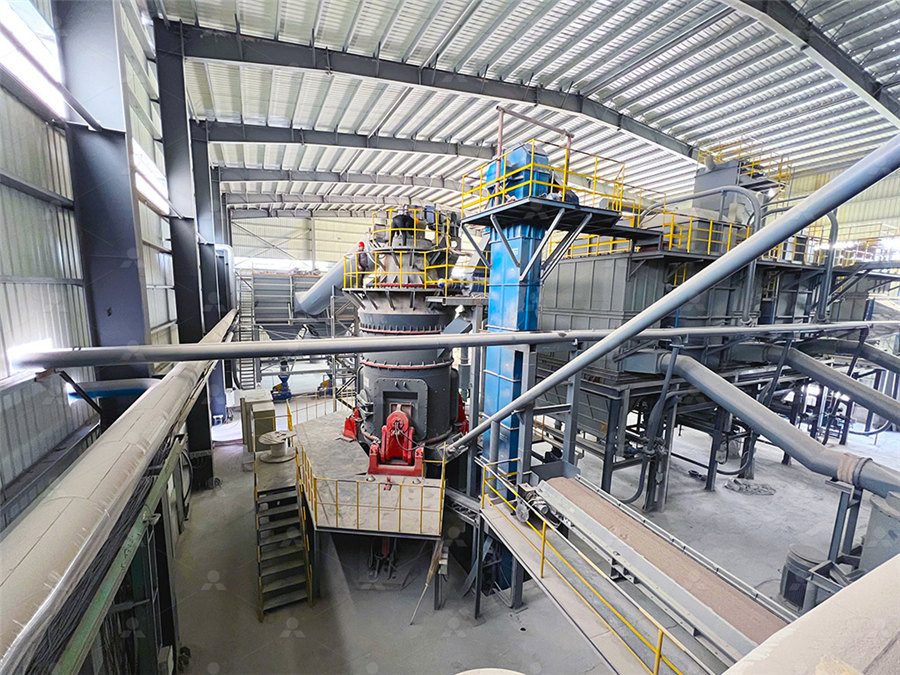
SAG Mill Grinding Circuit Design 911Metallurgist
2016年6月6日 The ability to mill a broad range of ore types in various circuit configurations, AG/SAG mills as a primary grinding stage in a circuit with or without additional stages of comminution; SAG mills have a higher installed power 2018年4月17日 Mill Sizing: After laboratory and pilot plant testing confirm the feasibility of autogenous or semiautogenous grinding, it can be used to establish the exact grinding circuit and mill sizeIn the pilot plant tests, the tare power of the pilot plant mills should be determined before and after each test run The tare power should be for the empty millAutogenous and SAG SemiAutogenous Mill Design CalculationsFind your ore mill easily amongst the 42 products from the leading brands (Fritsch GmbH, Retsch, Eriez, Motor power: 4 kW Ball mill is common used grinding plant in the industry, Ore mill, Ore grinding mill All industrial manufacturers2018年5月2日 Coal mill malfunctions are some of the most common causes of failing to keep the power plant crucial operating parameters or even unplanned power plant shutdowns Therefore, an algorithm has been developed that Detection of Malfunctions and Abnormal Working
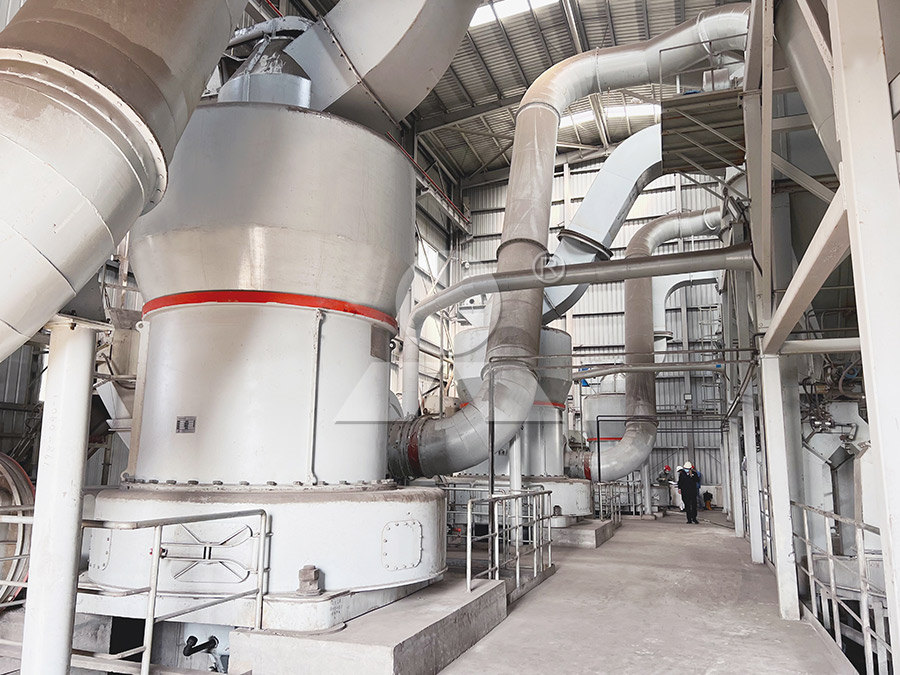
Derivation and validation of a coal mill model for control
2012年5月1日 Coal fired power plants are heavily used due to large and long lasting coal resources compared with oil or natural gas An important bottleneck in the operation of this particular kind of plants, however, is the coal pulverization process, which gives rise to slow takeup rates and frequent plant shutdowns (Rees Fan, 2003)In typical coal fired power plants, pellets for power stations 1992 Central coal grinding plant (LM 263 D) for the production of lignite (brown) coal dust 1985 Delivery of first selfinerting coal grinding plant (LM 212 D) for the steel industry 1980 Delivery of first modular coal mill (LM 263 D) 1965 Construction of first pressure mill (LM 122 D) 1961 Introduction of Loesche Grinding Technology for the Power Industry2014年10月1日 In a test performed in the Loesche test center in Germany, copper slag grinding saved 229% energy in an airswept model and 344% energy in an overflow model [13,14]Copper Ore Grinding in a Mobile Vertical Roller Mill Pilot PlantThe coal output then moves towards the throat of the mill where it mixes with high speed hot primary RESULT AND DISCUSSION The measurement data used in the modeling of the process are obtained from North Chennai Thermal Power Plant (NCTPS) 6 MODEL PREDICTIVE CONTROLLER pressure drop across the mill, power consumed for grinding, (PDF) Modeling and Control of Coal Mill Academia
.jpg)
Modeling of Coal Mill System Used for Fault Simulation
2020年4月7日 In order to obtain massive fault sample data effectively, based on the analysis of primary air system, grinding mechanism and energy conversion process, a dynamic model of the coal mill system In an ore grinding plant, integrated control techniques 90 are used to maximize fresh ore throughput and minimize the consumed power while maintaining a speci ed grind in the milling productModeling and Simulation of Whole Ball Mill Grinding Plant for 2016年3月11日 In the crushing section, the ore as it comes from the mine is broken down dry to a size suitable for the wet grinding machines ; these can, if necessary, be made to take lumps of 2in size, but they work much more efficiently if their feed is ½ in or lessCrushing Plant Flowsheet DesignLayout 911MetallurgistHigh and continued increases in electricity costs, coupled with the everincreasing power consumption by primary grinding circuits due to declining head grades of orebodies, provides a compelling case for these technologies Additionally, the ability to successfully deploy stirred milling in coarse grinding applicationsTECHNOLOGY SELECTION OF STIRRED MILLS FOR ENERGY EFFICIENCY IN PRIMARY
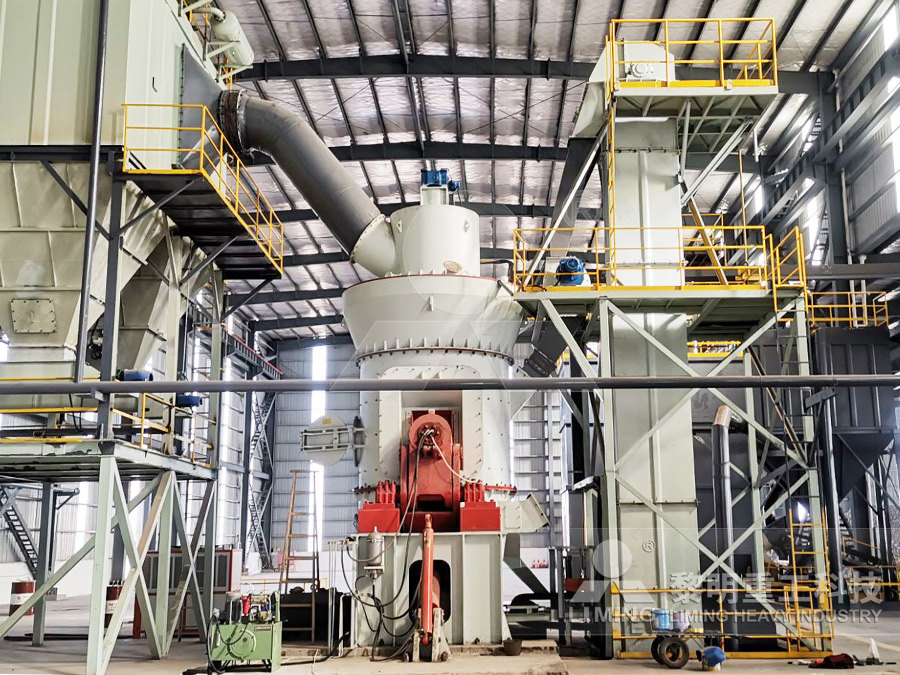
Limestone Grinding Mill That You Need To Know Mortar Plant
2023年9月19日 Limestone grinding mill Material: Limestone Finished product particle size: 01730044mm Processing capacity: 8176t/shift Applicable materials: calcium carbonate crushing processing, gypsum powder processing, power plant desulfurization, nonmetallic ore pulverizing, coal powder preparation, etc Main limestone grinding machines Vertical roller 2018年7月1日 The mill is the most power intensive element in a grinding mill circuit and the power draw of the mill motor is represented by P mill (Matthews and Craig, 2013) The slurry mixture of ground ore and water in the mill is discharged into the sump through an enddischarge screen that limits the particle size of the discharged slurryHybrid nonlinear model predictive control of a runofmine ore 2016年9月1日 SAG mill power draw models are used in mill design and grinding circuit modelling to predict how much power will be consumed by a particular mill geometry and operating configurationAN UPDATED DATA SET FOR SAG MILL POWER 1992年1月1日 Mill power draw can be predicted with reasonable accuracy for a known mill geometry, speed, and filling contents (Hogg Fuersteneau 1972; Morrell, 1993)Because plants constantly measure the mill (PDF) Prediction of grindingmill power
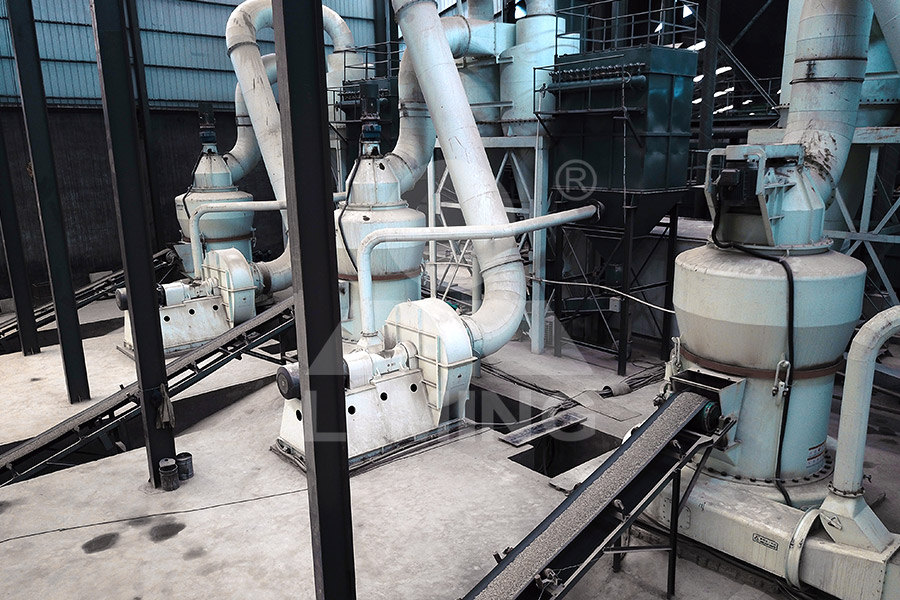
Analysis and validation of a runofmine ore grinding mill circuit
2013年4月1日 Two types of mills commonly found in the minerals processing industry are ball and semiautogenous (SAG) mills, which use both ore and steel balls as grinding media (Wei and Craig, 2009b)In the case of a ball mill the ore is crushed before it enters the mill, whereas a SAG mill receives runofmine (ROM) ore directly (Stanley, 1987)A SAG mill in a singlestage 2017年5月8日 Coming now to a study of the effect of the density of the grinding media upon the power required to drive a mill it follows that since the mass of grinding bodies has a definite configuration, as suggested by Fig 33, then the torque to drive the mill will be proportional to the weight of the charge; that is, without powder, proportional to the density of the material of the Grinding Mill Power 911Metallurgist2022年8月31日 Dear Colleagues, The grinding process, as a primary stage of ore/raw material processing, is a necessary operation in beneficiation plants It not only provides the appropriate particle size for subsequent separation operations but also enables the liberation of valuable minerals from the gangueGrinding Modeling and Energy Efficiency in Ore/Raw Material Ore grinding can account for 60% of a site’s electrical power load and electricity accounts for 38% of Barrick’s total energy and the primary ore grinding consumes about 55% of the electricity and is associated with million tonnes per year of 17 Ball mill power reduction 0 : 09 3,000,000 : 2,000 Net Savings : 19,600,000 IMPROVING ENERGY EFFICIENCY IN BARRICK GRINDING CIRCUITS
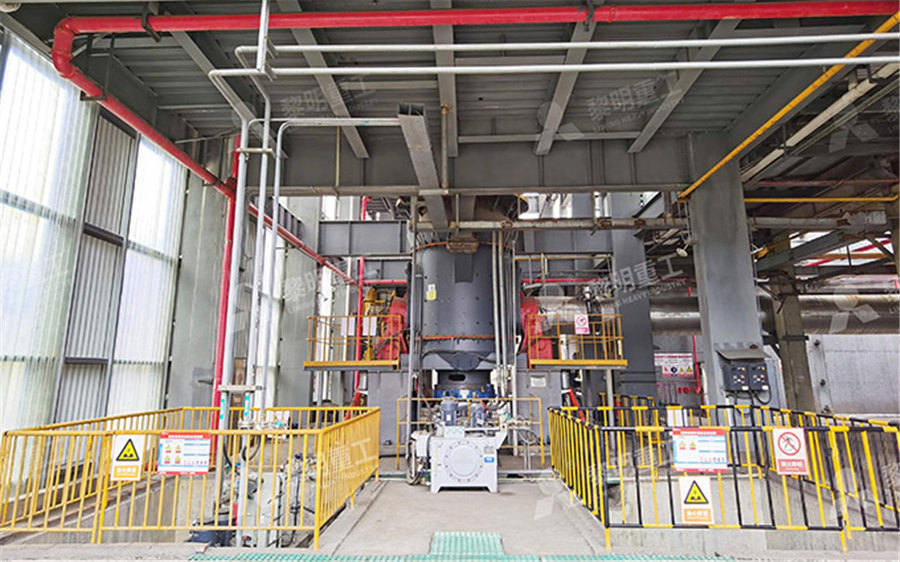
PlantWide Control Framework for a Grinding Mill Circuit
2019年3月2日 A total of 61 works published in the primary literature, Process and power plant control, A simple and novel nonlinear model of a runofmine ore grinding mill circuit, 2020年10月20日 Tracking the mill performance showed that the mill power consumption decreased from 949 to 663 kWh/t (a nearly 30% reduction), P 80 of the mill product decreased from 611 to 355 μm, and the mill fresh feed flow rate increased from 511 to 521 t/h by decreasing the feed ore hardness from 112 min to 58 min based on SAG power index (SPI)The performance improvement of a fullscale autogenous mill by setting Prediction and optimization of tower mill grinding power was used in a comminution circuit instead of the energyinefficient ball mill in the copperleadzinc ore processing plant after the primary jaw crusher the backpropagation “BP” neural network algorithm was employed to model and optimize the grinding processes of Prediction and optimization of tower mill grinding power 2015年11月1日 Most of the power plants employ simple mill controls, primary air temperature, and power consumption Download: Download highres image (317KB) Download: Download fullsize image; Fig 7 Model inputs from 2203 Mathematical model of a roller mill for fuel grinding and drying in coalfired power stations, in: Aufbereitungs A unified thermomechanical model for coal mill operation
.jpg)
Relationship between SAG mill power draw, bearing
Download scientific diagram Relationship between SAG mill power draw, bearing pressure and feed rate from publication: Supervisory Fuzzy Expert Controller for SAG Mill Grinding Circuits: Sungun 2015年6月19日 The basic parameters used in ball mill design (power calculations), rod mill or any tumbling mill sizing are; material to be ground, characteristics, Bond Work Index, bulk density, specific density, desired mill Ball Mill Design/Power Calculation 911MetallurgistDarreh gold processing plant is collected for modeling SAG mill power The processing plane is located 32 km north of Takab city in West Azarbaijan province, Iran The ore is supplied from the Aq Darreh mine 12 km from the plant In the grinding of Aq Darreh gold processing, the ore is fed to the SAG mill for grinding after crushingSemiautogenous mill power prediction by a hybrid neuralIntroduction The main Function of the Pulveriser in thermal power plant is to crush/grinding the raw coal coming from coal handling system through coal feeder into a predetermined size in order to increase the surface area of the coal If the coal is not pulverised, the coal might not burn completely, thus resulting in wastage of fuelPulveriser in Thermal Power Plant Bowl Mill Ball Mill
.jpg)
Fine Grinding A Refresher 911 Metallurgist
Many powerbased grinding models exist, and most operators are familiar with Fred Bond's "third theory" Bond's model is most commonly used to describe primary and secondary grinding to product sizes above, for example, 100 µm Operators sometimes use Bond's equation to INTRODUCTION Primary grinding mills as defined in this paper, are autogenous or semiautogenous rotating, tumbling mills having a coarse feed with a top size usually varying from 150 to 300 mm (6 to 12 inches) Most frequently, the feed to these mills is the product of primary crushing plants but in some cases run of mine ore is used as feed such as at Benguet, Primary Grinding Mills: Selection, Sizing And Current PracticesGrinding Mills Barry A Wills, James A Finch FRSC, FCIM, PEng, in Wills' Mineral Processing Technology (Eighth Edition), 2016 71 Introduction Grinding is the last stage in the comminution process where particles are reduced in size by a combination of impact and abrasion, either dry, or more commonly, in suspension in waterGrinding Mill an overview ScienceDirect TopicsRequest PDF On Mar 15, 2015, Mathis Reichert and others published Research of iron ore grinding in a verticalrollermill Find, read and cite all the research you need on ResearchGateResearch of iron ore grinding in a verticalrollermill
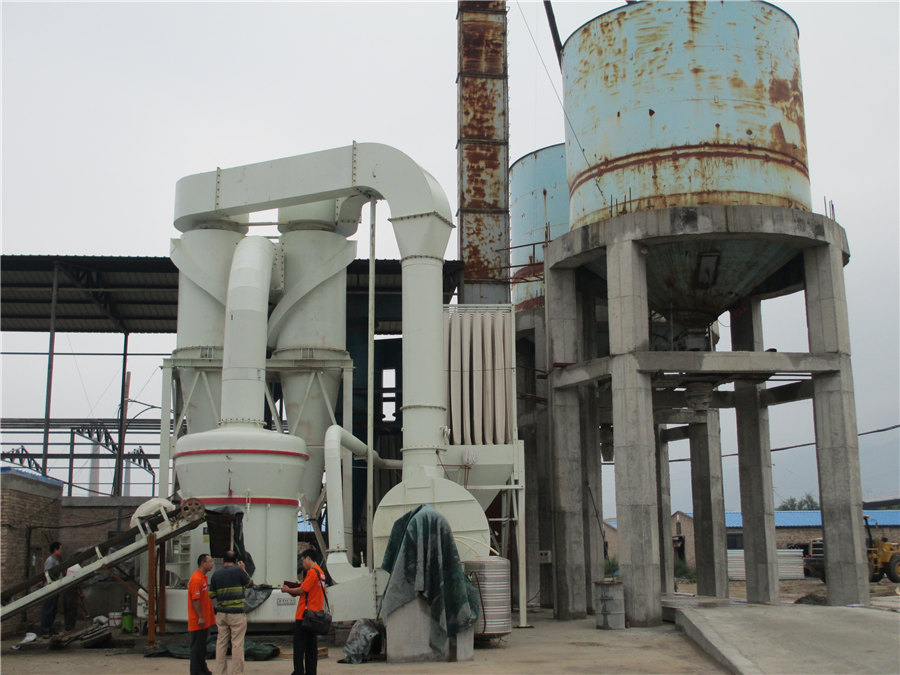
Analysis and validation of a runofmine ore grinding mill circuit
2013年4月1日 A simple and novel nonlinear model of a runofmine ore grinding mill circuit, developed for process control and estimation purposes, is validated